Turbidity barriers, also known as silt curtains, silt booms, or sediment curtains, are temporary, in-water barriers used for erosion and sediment control. These barriers consist of a geotextile fabric curtain that hangs vertically in the water, supported by floats at the surface and weighted at the bottom.
Purpose of Turbidity Barriers
The primary purpose of a turbidity barrier is to contain sediment and control erosion in water bodies during land disturbance activities or marine construction projects. By preventing sediment from spreading downstream, these barriers protect marine life and maintain water quality.
Conditions for Turbidity Barrier Use
Turbidity barriers are essential whenever construction activities in tidal or non-tidal waters risk causing silt and sediment displacement. They are particularly useful in:
- Marine construction sites
- Dredging operations
- Bridge and pier construction
- Shoreline restoration projects
- Any in-water work that disturbs sediment
Planning Considerations for Effective Turbidity Barriers
Marine construction often leads to soil erosion and increased suspended particles in water. This suspended sediment can travel and negatively impact water turbidity and marine ecosystems, affecting fish behavior and the overall health of aquatic life. Turbidity curtains are designed to contain this sediment within the immediate construction zone.
Water flow conditions are a crucial factor in selecting the right turbidity barrier. This guide focuses on situations with minimal to moderate flow, up to 5 feet per second (approximately 3 knots). For higher flow conditions, consulting with specialists like Enviro-USA is recommended.
Water direction is also critical. Turbidity barriers are designed to trap sediment, not block water flow. Therefore, they should not be installed across strong channel flows.
In moving water environments like rivers or shorelines, it’s vital to account for water level fluctuations due to tides or rising water. Anchoring systems must be designed to accommodate these changes to prevent the barrier from submerging. Permeable skirts are advisable for curtains intended for long-term placement in dynamic water conditions. These permeable fabrics allow water to pass through while retaining sediment within the work area. Water flow rate and sediment particle size should be considered when choosing a permeable fabric.
Sediment removal behind the barrier is an option, but it should be done carefully to avoid re-suspending particles, especially if regulatory authorities require it.
Before removing a turbidity barrier, allow sediment to settle for at least 12-24 hours to minimize disturbance and turbidity.
Design Criteria for Turbidity Barriers
Types of Turbidity Barriers
The industry generally recognizes three types of turbidity curtains, categorized by their duty level and suitability for different water conditions:
Type I Turbidity Curtain (Light Duty)
Type I turbidity curtains are designed for calm, protected waters with no current and minimal wind or wave action. They are ideal for enclosed ponds, lakes, and sheltered marina environments.
Image alt text: Type 1 Light Duty Turbidity Curtain: Best selection for calm water sediment control, manufactured by Enviro-USA.
Type II Turbidity Curtain (Medium Duty)
Type II turbidity curtains are built for areas with small to moderate currents (up to 2 knots or 3.5 feet per second) and some exposure to wind and waves. These are suitable for slow-moving streams, protected harbors, and areas with moderate wave action.
Image alt text: Type 2 Medium Duty Turbidity Curtain: Ideal selection for moderate current and wave conditions in marine construction projects.
Type III Turbidity Curtain (Heavy Duty)
Type III turbidity curtains are heavy-duty barriers designed for significant currents (up to 3 knots or 5 feet per second), tidal wave action, and strong winds. They are appropriate for use in open coastal areas, tidal zones, and environments with harsh weather conditions.
Image alt text: Type 3 Heavy Duty Turbidity Curtain: Robust selection for heavy currents and tidal waters, ensuring effective sediment containment.
After determining the water conditions and selecting the appropriate turbidity barrier type, further design criteria are necessary for proper system implementation.
Depth Considerations for Turbidity Curtains
In non-tidal areas or locations without significant wind or wave forces, the turbidity barrier should ideally extend to the full depth of the water body to maximize sediment containment.
However, in tidal or wave-prone areas, the curtain should not reach the bottom. A gap of at least 1 foot should be maintained between the skirt and the seabed. This prevents the curtain’s movement from stirring up bottom sediments due to tidal motion. In deeper waters, skirt depths are generally limited to 10-12 feet. Deeper skirts increase stress on the mooring system and can cause billowing, reducing the effective depth and overall curtain performance.
Placement and Layout Strategies
Placing turbidity curtains parallel to the water flow direction minimizes stress on the system. Figure 1 illustrates typical layouts for protected waters (streams, ponds, lakes) versus tidal or high-energy waters (harbors, shorelines).
Image alt text: Turbidity Curtain Layout and Anchoring Diagram: Illustrative selection for optimal placement in varying water conditions, including anchoring methods.
Total Length and Section Length
When determining the barrier length, adding 10-20% extra length is advisable to accommodate measurement errors, simplify installation, and reduce stress from waves and currents.
While turbidity barrier sections can be connected, minimizing joints enhances stability. Industry standards often use 50-foot sections, with lengths rarely exceeding 100 feet for stability. Enviro-USA offers turbidity curtains in permeable or impermeable skirts, in 50 & 100 ft sections, and custom lengths up to 100 feet.
Anchoring Systems for Turbidity Barriers
The stability of a turbidity barrier heavily relies on secure anchoring to land and/or water. Both ends of the barrier, floating and weighted, must extend adequately into the shoreline to fully enclose the work area. Trees or solid structures can serve as anchor points on land.
Permeable vs. Impermeable Skirts
For stagnant water with minimal flow into the containment area, impermeable fabric can be used to create a solid barrier. However, turbidity curtains are not dams and should not be expected to block significant water flow. Generally, their purpose is to isolate the work area and allow sediment to settle. Therefore, permeable skirts are typically preferred. Always consult the manufacturer’s specifications to understand the permeability of the chosen curtain fabric.
Construction Specifications for Turbidity Barriers
1. Color: Turbidity barriers should be brightly colored, such as yellow or orange, to ensure visibility for boaters and other watercraft.
2. Curtain Skirt Fabric: The fabric must meet minimum specifications for thickness, weight, tensile strength, and UV resistance. (See Table 1).
3. Seams: All seams should be either thermally welded or sewn for maximum strength and durability.
4. Floats: Flotation devices must be flexible, buoyant, and enclosed in individual sleeves or collars attached to the curtain. Buoyancy must be sufficient to support the curtain’s weight and maintain at least a 3-inch freeboard above the waterline.
5. Load Lines: Load lines are required at the bottom of all turbidity barriers. Type II and Type III barriers also need top load lines. The top load line should be a vinyl-sheathed steel cable with a breaking strength exceeding 10,000 pounds. The bottom load line is typically a chain within the bottom hem, providing ballast to keep the curtain vertical. Load lines must have connectors capable of achieving the full breaking strength when joining sections.
6. Anchors: Two main types of anchoring systems are used:
- 6.1 Land Anchors: Typically include marine-grade universal connectors, poly rope, and 15” or 30” ground auger anchors. Type I applications often only require land anchors.
- 6.2 Water Anchors: Consist of an anchor (grappling hook, plow, or fluke-type), leader chain, nylon rope, a heavy-duty marker buoy, and approximately 6 feet of painted line. Water anchors are generally necessary for Type II and Type III curtains in moving water. For Type III applications in tidal areas, anchor lines must have enough slack to accommodate tidal changes without pulling the curtain down.
Table 1: Turbidity Barrier Skirt Fabric Requirements
Physical Property | Requirement |
---|---|
Thickness, mils | 45 |
Weight in ounces per square yard | |
– Type I | 18 |
– Type II | 18 or 22 |
– Type III | 22 |
Grab Tensile Strength, lbs. | 300 for 18oz and 500 for 22oz |
UV Inhibitor | Must be included |
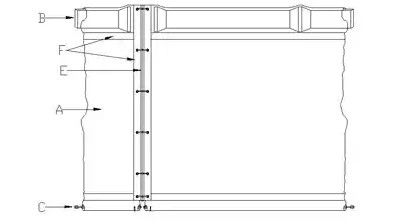
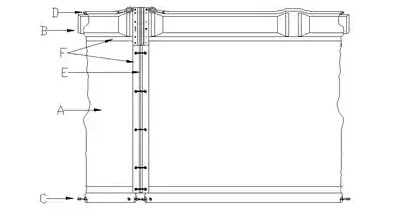
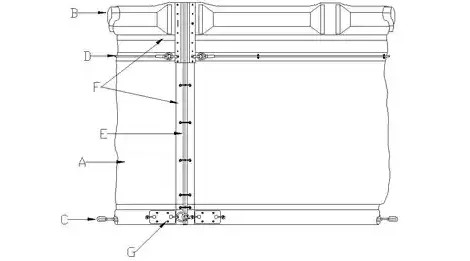
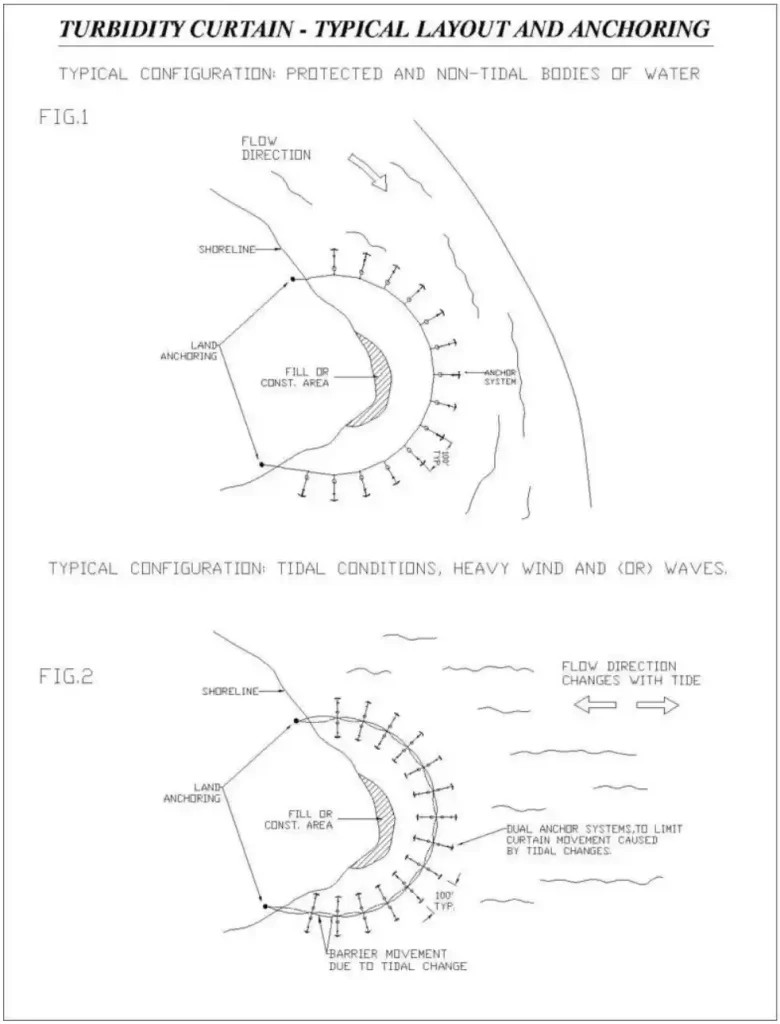
Installation Procedures for Turbidity Barriers
Calm Water (Type 1) Installation: Begin by setting end stakes and land anchors. Tow the furled turbidity barrier and attach it to these anchor points. Once secured, cut the furling lines to unfurl the skirt.
Moving Water (Type 2 or Type 3) Installation: First, set all anchors, including anchor buoys, ensuring they have adequate holding power for the expected current or tidal conditions. For tidal areas, install anchors on both sides of the curtain to handle bidirectional currents. With anchors in place, tow the furled curtain, securing it to the upstream anchor point first, then sequentially to each downstream anchor. After verifying position, buoyancy, and anchor security, cut the furling lines to deploy the skirt.
When using water anchors, always attach them to the flotation device, never to the skirt, to prevent damage. Refer to Figure 1 for typical installation layouts.
Maintenance of Turbidity Barriers
- Regular maintenance is essential to ensure continuous watercourse protection.
- Inspect turbidity curtains daily, with increased monitoring during storms or high flow/wind events.
- Any visible plume of cloudy water bypassing the curtain indicates inadequate performance. Immediately modify, adjust, or repair the barrier. Consult the manufacturer for repair kits if needed.
- Turbidity curtains should remain in place until construction is complete and water turbidity within the enclosed area is reduced to acceptable levels.
Removal Process for Turbidity Barriers
- Remove turbidity curtains in a manner that minimizes sediment release.
- If directed, remove sediment accumulated behind the curtain before removing the barrier itself. Allow any resulting turbidity to settle before proceeding.
- Choose a removal site free of sharp objects to prevent damage to the curtain during removal and hauling.
- For curtains with deep skirts, furl the skirt before removal from the water.
- Remove the curtain within 72 hours after water turbidity has returned to acceptable levels.
For further inquiries about turbidity barriers, or for state-specific D.O.T. specifications, please contact Enviro-USA American Manufacturer LLC. We are ready to assist with your turbidity control needs.