A beginner’s guide to kiln formed glass fused slumped cast introduces you to the captivating world of glass artistry, combining fusing, slumping, and casting techniques. At CONDUCT.EDU.VN, we offer insights into this exciting craft, providing a pathway to creating unique glass art, ensuring ethical creation. Explore the art of glasswork, kiln formed glass, and glass fusing with detailed guides on annealing and expert advice.
1. Understanding Kiln Formed Glass: An Introduction
Kiln formed glass is an umbrella term encompassing various techniques where glass is heated in a kiln to achieve a desired shape or design. It’s a versatile art form that allows for immense creativity and customization. This guide will explore the primary methods within kiln forming: fusing, slumping, and casting.
1.1. What is Glass Fusing?
Glass fusing is the process of joining compatible glass pieces together by heating them in a kiln until they meld into a single, unified piece. This technique allows artists to create intricate patterns, vibrant colors, and unique textures. The process involves carefully selecting compatible glass, arranging it to your desired design, and then firing it in a kiln according to a specific schedule. This schedule controls the heating and cooling rates to ensure a strong and stable final product.
1.2. What is Glass Slumping?
Glass slumping, often a secondary step after fusing, involves heating a piece of glass until it softens and conforms to the shape of a mold placed beneath it. This technique is used to create functional pieces like bowls, plates, and decorative forms with curved surfaces. The mold can be made of various materials, including ceramic, stainless steel, or even sand, each offering different textures and effects. The slumping process requires precise temperature control to prevent the glass from over-bending or cracking.
1.3. What is Glass Casting?
Glass casting is a technique where molten glass is poured into a mold and allowed to cool and solidify. This method is ideal for creating three-dimensional objects, sculptures, and intricate designs. There are several casting methods, including:
- Lost Wax Casting: This process involves creating a wax model, encasing it in a mold, melting out the wax, and then filling the resulting cavity with molten glass.
- Sand Casting: A mold is created in sand, and molten glass is poured directly into the mold.
- Pate de Verre: This technique involves packing crushed glass frit into a mold and then firing it in a kiln to fuse the glass particles together.
1.4. Key Differences Between Fusing, Slumping, and Casting
Technique | Description | Typical Applications | Skill Level |
---|---|---|---|
Fusing | Joining glass pieces by heating them until they melt together. | Decorative panels, jewelry, coasters, small sculptural elements | Beginner to Advanced |
Slumping | Shaping glass by heating it until it conforms to a mold. | Bowls, plates, platters, decorative forms | Beginner to Intermediate |
Casting | Pouring molten glass into a mold to create a three-dimensional object. | Sculptures, architectural elements, unique art pieces | Intermediate to Advanced |
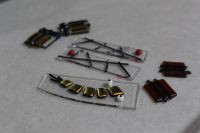
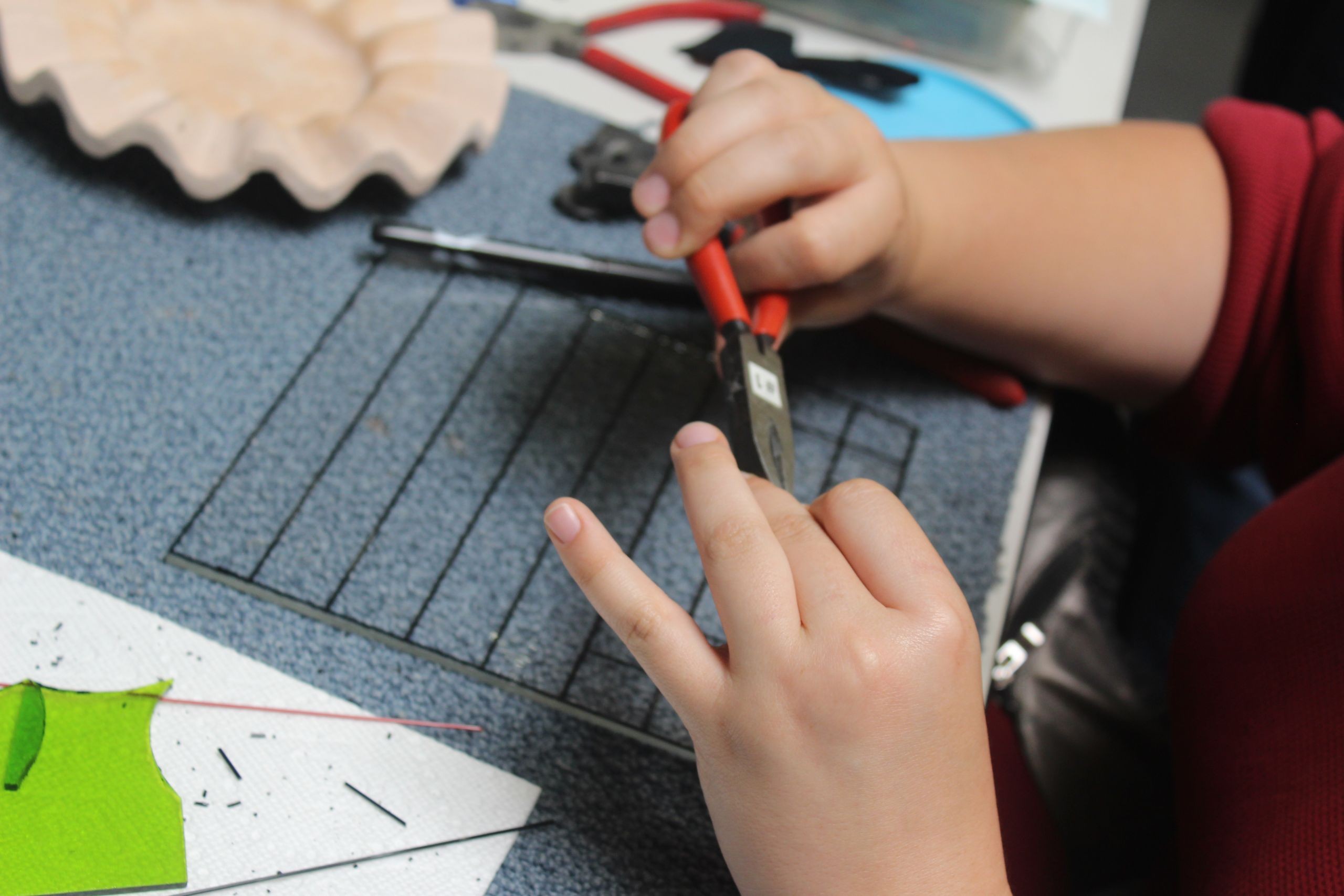
Understanding these key differences will help you choose the right technique for your desired project.
2. Essential Equipment and Tools for Kiln Formed Glass
Embarking on your kiln formed glass journey requires the right equipment. Here’s a breakdown of the essential tools and machinery you’ll need:
2.1. The Kiln: Your Central Tool
A kiln is the heart of any kiln forming glass endeavor. It’s an insulated oven capable of reaching and maintaining high temperatures necessary to melt and shape glass. When selecting a kiln, consider the following factors:
- Size: Choose a kiln size that suits the scale of your projects. Smaller kilns are suitable for jewelry and small decorative items, while larger kilns are necessary for larger artworks.
- Temperature Range: Ensure the kiln can reach the temperatures required for the types of glass you plan to work with. Most glass fusing and slumping projects require temperatures between 1350°F and 1700°F (730°C and 930°C).
- Controller: A programmable controller allows you to precisely control the firing schedule, including heating rates, hold times, and cooling rates. This is crucial for achieving consistent and predictable results.
2.2. Glass Cutting Tools
Accurate glass cutting is vital for successful fusing and slumping projects. The essential tools include:
- Glass Cutter: A handheld tool with a small, hardened wheel used to score the surface of the glass.
- Running Pliers: Used to apply pressure along the score line to create a clean break.
- Grozing Pliers: Used to nibble away small pieces of glass to refine the shape.
- Safety Glasses: Protect your eyes from flying glass shards.
2.3. Grinding and Coldworking Equipment
Grinding and coldworking are necessary to refine the edges and surfaces of your glass pieces:
- Glass Grinder: A machine with a rotating grinding wheel used to smooth and shape the edges of the glass.
- Diamond Hand Pads: Used for hand-grinding and polishing.
- Wet Belt Sander: For smoothing larger surfaces and removing imperfections.
2.4. Kiln Furniture and Accessories
Kiln furniture provides a stable and protective surface for your glass during firing:
- Kiln Shelves: Heat-resistant shelves that support your glass projects inside the kiln.
- Kiln Posts: Used to elevate shelves and create stacking configurations.
- Kiln Wash or Shelf Primer: A coating applied to kiln shelves to prevent glass from sticking.
- Molds: Used in slumping and casting to create specific shapes.
2.5. Safety Gear
Safety should always be a top priority when working with glass and kilns:
- Heat-Resistant Gloves: Protect your hands from burns when handling hot glass or kiln furniture.
- Safety Glasses: Shield your eyes from flying glass and debris.
- Dust Mask: Prevents inhalation of glass dust during grinding and coldworking.
- Well-Ventilated Workspace: Ensures adequate air circulation to remove fumes and dust.
2.6. Additional Tools and Materials
- Glass: Compatible glass sheets, frits, stringers, and other decorative elements.
- Adhesives: For tack-fusing glass pieces together before firing.
- Markers: For marking and designing on glass.
- Rulers and Templates: For precise cutting and shaping.
Equipping yourself with these essential tools and materials will set you up for success in the world of kiln formed glass. Always prioritize safety and follow manufacturer’s instructions for all equipment.
3. Choosing the Right Glass for Kiln Forming
Selecting the right type of glass is paramount for successful kiln forming. Compatibility is key to preventing cracking or breakage during the heating and cooling process.
3.1. Understanding Coefficient of Expansion (COE)
The Coefficient of Expansion (COE) measures how much a material expands or contracts in response to temperature changes. For glass fusing, it’s crucial to use glass with the same or very similar COE. If glasses with significantly different COEs are fused together, the stress created during cooling can lead to cracking or shattering.
3.2. Common Types of Glass for Kiln Forming
- Bullseye Glass: A popular choice for fusing and slumping due to its consistent quality, wide range of colors, and known COE (typically 90).
- Spectrum System 96 Glass: Another reliable option with a COE of 96, offering a diverse palette of colors and textures.
- Float Glass: Commonly used for windowpanes, float glass can be fused, but it requires careful temperature control and may not be compatible with other types of glass.
3.3. Identifying Glass Compatibility
- Manufacturer Specifications: Always refer to the manufacturer’s specifications to determine the COE of the glass.
- Compatibility Testing: Before embarking on a large project, it’s wise to conduct a small compatibility test by fusing together pieces of the glass you intend to use. Observe the fused piece for any signs of stress or cracking after cooling.
3.4. Forms of Glass
- Sheet Glass: The most common form, available in various colors, textures, and thicknesses.
- Frit: Crushed glass, available in different sizes from coarse to fine, used for creating textured surfaces and patterns.
- Stringers: Thin rods of glass used for adding fine lines and details.
- Noodles and Confetti: Decorative glass elements for adding unique visual effects.
3.5. Working with Dichroic Glass
Dichroic glass is a type of glass that has a thin, metallic coating applied to its surface, giving it a shimmering, iridescent appearance. It’s often used as an accent in fused glass projects. When working with dichroic glass, keep the following in mind:
- Orientation: The dichroic coating is on one side of the glass. Consider the orientation when layering the glass to achieve the desired effect.
- Firing Temperature: Dichroic coatings can be sensitive to high temperatures. Follow the manufacturer’s recommendations for firing schedules.
3.6. Tips for Choosing Glass
- Start with a Single Brand: When starting out, stick to a single brand of glass with a known COE to minimize compatibility issues.
- Document Your Materials: Keep a record of the types of glass you use, their COEs, and the firing schedules you employ. This will help you replicate successful results and troubleshoot problems.
- Consider the Desired Effect: Choose glass colors and textures that complement your design and achieve the desired visual impact.
By understanding the properties of different types of glass and carefully considering compatibility, you can ensure the structural integrity and aesthetic appeal of your kiln formed glass creations.
4. Mastering the Firing Schedule for Kiln Formed Glass
The firing schedule is the blueprint for your kiln’s behavior during the heating and cooling process. It’s a sequence of temperature changes and hold times that dictate how the glass melts, fuses, and anneals. A well-designed firing schedule is crucial for achieving successful and consistent results.
4.1. Understanding the Stages of a Firing Schedule
A typical firing schedule consists of several stages:
- Ramp-Up: The rate at which the kiln heats up, measured in degrees per hour (°F/hr or °C/hr).
- Soak/Hold: Maintaining a specific temperature for a set period of time to allow the glass to fuse or slump.
- Annealing: Slowly cooling the glass to relieve internal stress.
- Cool-Down: The final cooling phase, which can be controlled or allowed to occur naturally.
4.2. Factors Influencing the Firing Schedule
Several factors influence the ideal firing schedule for your project:
- Type of Glass: Different types of glass have different melting points and annealing temperatures.
- Thickness of Glass: Thicker glass requires longer soak times to ensure even heating and fusing.
- Size of Project: Larger projects require more gradual heating and cooling to prevent thermal shock.
- Desired Effect: The firing schedule can be adjusted to achieve different effects, such as a full fuse (completely smooth surface) or a tack fuse (glass pieces retain some of their individual shapes).
4.3. Sample Firing Schedule for Fusing Bullseye 90 Glass (Example)
This is a general guideline and may need adjustments based on your specific kiln and project:
Stage | Temperature (°F) | Ramp Rate (°F/hr) | Hold Time (Minutes) |
---|---|---|---|
Ramp-Up 1 | 250 | 250 | 30 |
Ramp-Up 2 | 1450 | 400 | 20 |
Soak | 1450 | – | 15 |
Anneal | 900 | 100 | 60 |
Cool-Down | 700 | 150 | 0 |
End | Room Temperature | – | – |
- Ramp-Up 1: Slowly preheats the kiln to prevent thermal shock.
- Ramp-Up 2: Rapidly increases the temperature to the fusing range.
- Soak: Allows the glass to fully fuse together.
- Anneal: Slowly cools the glass through the annealing range to relieve stress.
- Cool-Down: Allows the kiln to cool to room temperature.
4.4. Annealing: Relieving Stress in Glass
Annealing is a critical step in the firing schedule. It involves holding the glass at a specific temperature (the annealing point) for a period of time, then slowly cooling it. This process allows the glass molecules to relax and relieve internal stress, making the finished piece stronger and less prone to cracking.
4.5. Monitoring and Adjusting the Firing Schedule
- Kiln Thermocouple: A sensor that measures the temperature inside the kiln.
- Observation: Carefully observe the glass during firing (if possible) to ensure it’s melting and fusing as expected.
- Adjustments: Be prepared to adjust the firing schedule based on your observations and the results of previous firings.
4.6. Importance of Accurate Programming
Ensure your kiln controller is programmed accurately. Double-check all temperature settings, ramp rates, and hold times before starting the firing. Incorrect programming can lead to under-fired or over-fired pieces, or even damage to your kiln.
Mastering the firing schedule is an ongoing learning process. Experimentation and careful observation are key to developing firing schedules that work best for your kiln, your glass, and your artistic vision. Always consult the glass manufacturer’s recommendations for suggested firing schedules.
5. Step-by-Step Guide to Basic Glass Fusing
Now that you have a foundational understanding of the equipment, materials, and firing schedules, let’s walk through the basic steps of glass fusing:
5.1. Preparing Your Workspace
- Clean Surface: Ensure your work surface is clean and free of debris.
- Tools at Hand: Gather all necessary tools, including a glass cutter, running pliers, grozing pliers, safety glasses, and a marker.
- Kiln Preparation: Prepare your kiln shelf by applying a thin, even coat of kiln wash or placing a piece of kiln paper on the shelf. This will prevent the glass from sticking to the shelf during firing.
5.2. Cutting the Glass
- Design: Plan your design and determine the shapes and sizes of the glass pieces you’ll need.
- Scoring: Using a glass cutter, score the surface of the glass along the desired cut lines. Apply consistent pressure and listen for a smooth, even sound.
- Breaking: Use running pliers to apply pressure along the score line to create a clean break. For smaller pieces, you can gently tap the underside of the score line.
- Refining: Use grozing pliers to nibble away any unwanted edges or to refine the shape of the glass pieces.
5.3. Assembling the Design
- Arrangement: Carefully arrange the glass pieces on the prepared kiln shelf according to your design.
- Overlapping: If you want to create a layered effect, overlap the glass pieces slightly.
- Tack Fusing (Optional): For intricate designs, you can tack fuse the pieces together using a small amount of glue or by firing the piece at a lower temperature to lightly fuse the edges.
5.4. Firing the Kiln
- Placement: Carefully place the kiln shelf with the assembled glass into the kiln.
- Programming: Program the kiln controller with the appropriate firing schedule for the type and thickness of glass you are using.
- Monitoring: Monitor the kiln’s progress during firing.
- Cooling: Allow the kiln to cool completely before opening it. This may take several hours or even overnight.
5.5. Finishing Touches
- Inspection: Once the kiln has cooled, carefully remove the fused glass piece and inspect it for any sharp edges or imperfections.
- Grinding: Use a glass grinder or diamond hand pads to smooth any rough edges.
- Cleaning: Clean the fused glass piece with soap and water.
5.6. Optional Slumping
If you want to slump the fused glass piece into a mold, follow these steps:
- Mold Preparation: Prepare your mold by applying a mold release agent.
- Placement: Carefully place the fused glass piece on top of the mold.
- Slumping Firing: Fire the kiln according to a slumping schedule. This schedule will typically involve heating the glass to a lower temperature than fusing, allowing it to soften and conform to the shape of the mold.
- Cooling: Allow the kiln and the slumped glass piece to cool completely before removing it from the mold.
By following these steps, you can create beautiful and unique fused glass art. Remember to always prioritize safety and consult with experienced glass artists or instructors for guidance.
6. Exploring Glass Slumping Techniques
Glass slumping is a versatile technique that allows you to transform flat pieces of glass into elegant and functional forms. Here’s a closer look at the process:
6.1. Choosing the Right Mold
The mold is the defining element in glass slumping. Your mold dictates the final shape of your slumped glass piece. Molds can be made from a variety of materials, including:
- Ceramic Molds: Durable and reusable, ceramic molds are ideal for creating consistent shapes.
- Stainless Steel Molds: Offer a smooth, clean surface and are suitable for creating contemporary designs.
- Plaster Molds: Can be easily sculpted to create custom shapes.
- Sand Molds: Allow for unique textures and organic forms.
6.2. Preparing the Mold
Proper mold preparation is essential to prevent the glass from sticking to the mold during firing.
- Mold Release Agent: Apply a thin, even coat of mold release agent to the surface of the mold. Common mold release agents include kiln wash, boron nitride spray, and specialized slumping compounds.
- Drying: Allow the mold release agent to dry completely before placing the glass on the mold.
6.3. Slumping Firing Schedule
The slumping firing schedule is designed to heat the glass to a temperature where it softens and gradually conforms to the shape of the mold. A typical slumping firing schedule will look something like this:
Stage | Temperature (°F) | Ramp Rate (°F/hr) | Hold Time (Minutes) |
---|---|---|---|
Ramp-Up 1 | 250 | 250 | 30 |
Ramp-Up 2 | 1200 | 400 | 20 |
Soak | 1200 | – | 30-60 (Adjust as needed) |
Anneal | 900 | 100 | 60 |
Cool-Down | 700 | 150 | 0 |
End | Room Temperature | – | – |
- Adjusting Soak Time: The soak time will depend on the size and thickness of the glass, as well as the desired depth of the slump. Monitor the glass during firing and adjust the soak time accordingly.
6.4. Monitoring the Slumping Process
If possible, observe the glass through the kiln’s peephole during firing. This will allow you to monitor the slumping process and make adjustments to the firing schedule if necessary.
6.5. Cooling and Removing the Slumped Glass
- Complete Cooling: Allow the kiln and the slumped glass piece to cool completely before opening the kiln and removing the piece from the mold.
- Gentle Removal: Carefully remove the slumped glass piece from the mold. If the piece is stuck, gently tap the mold to release it.
- Cleaning: Clean the slumped glass piece with soap and water to remove any residual mold release agent.
6.6. Troubleshooting Slumping Issues
- Glass Sticks to the Mold: Ensure the mold is properly prepared with a mold release agent.
- Uneven Slumping: Adjust the firing schedule and ensure the mold is level.
- Cracking: Reduce the ramp rate and ensure the glass is properly annealed.
With practice and experimentation, you can master the art of glass slumping and create a wide variety of beautiful and functional glass objects.
7. Introduction to Glass Casting Techniques
Glass casting offers a pathway to create three-dimensional glass art. Let’s explore the fundamental casting techniques:
7.1. Lost Wax Casting
Lost wax casting, also known as cire-perdue, is a time-honored technique used to create intricate glass sculptures. Here’s an overview of the process:
- Wax Model: Create a detailed wax model of the desired glass object.
- Investing: Encase the wax model in a heat-resistant mold material, such as plaster or a specialized investment compound.
- Wax Removal: Melt out the wax from the mold, leaving a hollow cavity.
- Glass Filling: Place the mold in a kiln and fill the cavity with glass cullet (broken glass pieces).
- Firing: Fire the kiln according to a casting schedule, allowing the glass to melt and fill the mold completely.
- Cooling: Slowly cool the kiln to anneal the glass and prevent cracking.
- Divesting: Remove the mold material to reveal the cast glass object.
- Coldworking: Grind, polish, and refine the surface of the cast glass object.
7.2. Sand Casting
Sand casting is a more direct method of glass casting, where a mold is created in sand.
- Mold Creation: Pack sand tightly into a mold box around a pattern or object to create an impression.
- Glass Pouring: Carefully pour molten glass into the sand mold.
- Cooling: Allow the glass to cool slowly in the sand mold.
- Removal: Break away the sand mold to reveal the cast glass object.
- Coldworking: Grind, polish, and refine the surface of the cast glass object.
7.3. Pate de Verre
Pate de Verre, meaning “glass paste” in French, is a unique casting technique that involves packing crushed glass frit into a mold.
- Mold Creation: Create a mold from plaster or a similar material.
- Frit Packing: Carefully pack crushed glass frit into the mold, layering different colors to create intricate designs.
- Firing: Fire the kiln according to a pate de verre schedule, allowing the frit to fuse together.
- Cooling: Slowly cool the kiln to anneal the glass.
- Divesting: Remove the mold material to reveal the pate de verre object.
- Coldworking: Grind, polish, and refine the surface of the pate de verre object.
7.4. Considerations for Glass Casting
- Glass Type: Use glass specifically designed for casting.
- Mold Materials: Choose mold materials that can withstand high temperatures and won’t react with the glass.
- Firing Schedules: Follow carefully designed firing schedules to ensure proper melting and annealing.
- Safety: Wear appropriate safety gear when working with molten glass and hot kilns.
Glass casting offers a unique path to artistic expression, allowing you to create sculptural glass forms with depth, texture, and intricate detail.
8. Advanced Techniques in Kiln Formed Glass
Once you’ve mastered the basics of fusing, slumping, and casting, you can explore a range of advanced techniques to elevate your glass art:
8.1. Reactive Glass Techniques
Reactive glasses contain elements that react with each other when heated, creating unique colors and patterns at the interface between the glasses.
- Silver Glass: Glasses containing silver can react with sulfur in other glasses, producing a range of colors from yellows and oranges to reds and browns.
- Copper Glass: Glasses containing copper can react with other elements, creating blues, greens, and reds.
8.2. Incorporating Inclusions
Inclusions are objects embedded within the glass during fusing or casting. These can include:
- Metals: Copper, silver, and gold can be added to create unique visual effects.
- Enamels: Powdered glass that can be fused onto the surface of the glass to add color and detail.
- Ceramic Decals: Images printed on a special paper that can be fired onto the glass.
8.3. Pattern Bars
Pattern bars are created by fusing together multiple layers of glass to create a complex pattern. The resulting bar can then be sliced and fused into other projects.
8.4. Working with Murrine
Murrine are small, patterned glass elements that are created by layering molten glass and then pulling it into a cane. The cane is then sliced to reveal the pattern.
8.5. Kiln Casting with Multiple Molds
This technique involves creating multiple molds that fit together to form a complex three-dimensional object. Molten glass is poured into each mold, and the pieces are then fused together.
8.6. Using Powders and Frits for Surface Decoration
Glass powders and frits can be applied to the surface of fused or slumped glass to create a variety of decorative effects.
- Sifting: Using a sieve to apply a thin, even layer of powder.
- Stenciling: Using a stencil to create a pattern with powder.
- Painting: Mixing powder with a binder to create a paintable medium.
8.7. Coldworking Techniques
Coldworking techniques, such as grinding, polishing, sandblasting, and engraving, can be used to add texture and detail to finished glass pieces.
Exploring these advanced techniques will allow you to push the boundaries of your creativity and create truly unique and stunning kiln formed glass art.
9. Safety Practices for Kiln Formed Glass
Working with glass and kilns involves inherent risks. Prioritizing safety is crucial to preventing accidents and injuries.
9.1. Eye Protection
Always wear safety glasses or a face shield when cutting, grinding, or handling glass. Flying glass shards can cause serious eye injuries.
9.2. Hand Protection
Wear gloves when handling glass to protect your hands from cuts. Heat-resistant gloves are essential when handling hot glass or kiln furniture.
9.3. Respiratory Protection
Wear a dust mask or respirator when grinding or sandblasting glass to prevent inhalation of glass dust.
9.4. Kiln Safety
- Proper Ventilation: Ensure your kiln is properly ventilated to remove fumes.
- Heat-Resistant Clothing: Wear heat-resistant clothing when working around a hot kiln.
- Clearance: Maintain a safe distance from the kiln when it is firing.
- Kiln Maintenance: Regularly inspect and maintain your kiln to ensure it is in good working order.
9.5. Glass Handling
- Careful Lifting: Lift glass carefully and avoid sudden movements.
- Proper Support: Support large pieces of glass to prevent them from breaking.
- Clean Workspace: Keep your workspace clean and free of clutter to prevent tripping and falls.
9.6. Electrical Safety
- Grounded Outlets: Ensure your kiln is plugged into a grounded outlet.
- Proper Wiring: Use proper wiring and extension cords that are rated for the kiln’s amperage.
- Avoid Water: Never use water near electrical equipment.
9.7. First Aid
- Cuts: Clean cuts thoroughly with soap and water. Seek medical attention if the cut is deep or bleeding heavily.
- Burns: Cool burns immediately with cold water. Seek medical attention for severe burns.
- Eye Injuries: Flush eyes with water for 15 minutes. Seek medical attention immediately.
By following these safety practices, you can minimize the risks associated with kiln formed glass and enjoy the art form safely and responsibly.
10. Where to Learn More About Kiln Formed Glass
Ready to deepen your understanding and skills in kiln formed glass? Here are some resources to explore:
10.1. Online Courses and Tutorials
Many online platforms offer courses and tutorials on glass fusing, slumping, and casting.
- CreativeLive: Offers a variety of glass art courses taught by experienced instructors.
- Udemy: Provides a range of affordable courses on glass fusing and related techniques.
- YouTube: A wealth of free tutorials and demonstrations from glass artists around the world.
10.2. Workshops and Classes
Hands-on workshops and classes provide invaluable experience and personalized instruction.
- Local Art Centers: Check with your local art centers and community colleges for glass art classes.
- Glass Art Studios: Many glass art studios offer workshops and classes for beginners and experienced artists alike.
- The Crucible: A renowned industrial arts school offering comprehensive glass fusing and slumping programs.
10.3. Books and Magazines
- “Contemporary Warm Glass” by Brad Walker: A comprehensive guide to fusing, slumping, and casting.
- “Fused Glass Handbook” by Gil Reynolds: A practical guide to fusing techniques and projects.
- “Glass Art Magazine”: A publication showcasing contemporary glass art and techniques.
10.4. Online Communities and Forums
Connect with other glass artists, share your work, and ask questions in online communities and forums.
- Warm Glass: A popular online forum for glass artists.
- Facebook Groups: Search for glass fusing and slumping groups on Facebook.
10.5. Museums and Galleries
Visit museums and galleries to see examples of kiln formed glass art and gain inspiration for your own creations.
10.6. CONDUCT.EDU.VN
At CONDUCT.EDU.VN, we understand the challenges in finding reliable information on ethical standards. That’s why we offer comprehensive and easily accessible resources to guide you.
By taking advantage of these resources, you can continue to learn and grow as a kiln formed glass artist. Remember to be patient, persistent, and always prioritize safety.
Navigating the world of kiln formed glass can be challenging, with numerous techniques and safety considerations. At CONDUCT.EDU.VN, we simplify this journey by providing clear, concise guidance, ensuring ethical practices in your artistic pursuits.
For reliable and comprehensive information on ethical conduct and best practices, visit CONDUCT.EDU.VN or contact us at 100 Ethics Plaza, Guideline City, CA 90210, United States, Whatsapp: +1 (707) 555-1234.
Frequently Asked Questions (FAQ) About Kiln Formed Glass
Here are some frequently asked questions about kiln formed glass:
1. What is the difference between fusing and slumping?
Fusing involves joining pieces of glass together by heating them until they melt into a single piece. Slumping involves heating a piece of glass until it softens and conforms to the shape of a mold.
2. What is COE and why is it important?
COE stands for Coefficient of Expansion. It measures how much a material expands or contracts in response to temperature changes. Using glass with the same or very similar COE is crucial to prevent cracking or breakage during fusing.
3. What temperature do I fuse glass at?
The fusing temperature depends on the type of glass you are using. Generally, it ranges from 1350°F to 1700°F (730°C to 930°C).
4. What is annealing and why is it necessary?
Annealing is the process of slowly cooling glass to relieve internal stress. It is necessary to prevent cracking and ensure the strength and durability of the finished piece.
5. What is kiln wash and why do I need to use it?
Kiln wash is a coating applied to kiln shelves to prevent glass from sticking during firing.
6. Can I fuse different colors of glass together?
Yes, you can fuse different colors of glass together as long as they have the same or very similar COE.
7. Can I fuse glass at home?
Yes, you can fuse glass at home if you have a kiln and the necessary safety equipment.
8. How long does it take to fuse glass?
The firing time depends on the size and thickness of the glass, as well as the desired effect. It can range from a few hours to overnight.
9. What is dichroic glass?
Dichroic glass is a type of glass that has a thin, metallic coating applied to its surface, giving it a shimmering, iridescent appearance.
10. Where can I buy glass for fusing?
You can buy glass for fusing from online retailers, glass art supply stores, and some craft stores.
We hope this FAQ has answered some of your questions about kiln formed glass. If you have any further questions, please don’t hesitate to contact us at conduct.edu.vn, where we are committed to providing guidance and support for ethical conduct.
Remember, mastering kiln formed glass is a journey that requires patience, practice, and a commitment to safety. Embrace the challenges, celebrate your successes, and never stop learning. The world of glass art awaits your unique creations.