Design for Manufacturing (DFM) success is a critical element in modern product development, and a robust DFM strategy optimizes designs for efficient production while minimizing costs. At CONDUCT.EDU.VN, we understand the need for thorough planning and consideration, offering a definitive guide to navigating the complexities of DFM to ensure your projects are both manufacturable and successful. By integrating manufacturability with design, cost-effectiveness, and material selection early on, you’ll ensure streamlined production, reduced waste, and enhanced product quality.
1. Understanding the Core Principles of DFM
DFM is a methodology that emphasizes the importance of considering manufacturing constraints and capabilities during the design phase of a product. Unlike conventional design methods, DFM prioritizes manufacturability from the initial conceptualization stage, leading to significant savings in time and costs. According to a study by Siemens, early DFM implementation is critical for minimizing production challenges [1].
Key principles and concepts behind DFM include:
- Process Optimization: Refining manufacturing processes for each component, taking into account materials and tolerances.
- Design Simplification: Streamlining designs to reduce complexity, enhance production efficiency, and lower costs.
- Material Selection: Choosing materials that balance cost, quality, and performance for optimal manufacturability.
- Environmental Considerations: Evaluating the environmental impact of the product at every stage of its lifecycle.
- Testing and Validation: Ensuring the product meets or exceeds industry standards through rigorous testing.
DFM principles are applied across various industries to achieve specific objectives. For example, in the medical device industry, DFM ensures smooth surfaces and easy cleaning to meet regulatory standards and patient safety. In automotive engineering, DFM focuses on creating engine parts that are easily accessible and replaceable to minimize maintenance time and expenses. Aerospace DFM solutions aim to enhance fuel economy and performance by designing lighter and less complex aircraft components. These tailored approaches highlight the versatility and importance of DFM in diverse manufacturing contexts.
2. Cultivating a DFM Mindset for Enhanced Efficiency
Developing a DFM mindset is fundamental for maximizing supply chain efficiency. This involves understanding and implementing design and production constraints from the outset. By integrating limitations such as avoiding complex geometries and undercuts in injection molding designs, a DFM-centric approach helps maintain cost-effectiveness and keeps projects on track. Similarly, optimizing sheet metal designs with appropriate bend radii and nesting considerations prevents production issues, reducing the need for iterations and rework.
Adopting a DFM mindset has several benefits:
- Competitive Advantage: Faster product launches provide a competitive edge in the market.
- Adaptability: Greater agility to respond to changing market demands.
- Customer Satisfaction: Enhanced ability to meet customer expectations.
- Brand Loyalty: Improved product quality fosters brand credibility and customer loyalty.
- Waste Reduction: Streamlined processes minimize waste throughout the supply chain.
Collaboration across disciplines is essential for fostering a DFM mindset. When engineers and designers work closely together, they can identify potential manufacturing issues early in the design process. Sharing notifications about design changes that improve cost-effectiveness is crucial for effective DFM implementation. Organizations can also promote DFM principles by cultivating a culture of continuous improvement, including regular design reviews and feedback from manufacturing teams. Utilizing state-of-the-art design and simulation tools, such as computer-aided design (CAD) software with integrated DFM analysis capabilities, enables designers to proactively optimize designs by evaluating moldability, assembly feasibility, and material selection.
Finally, fostering a DFM mindset requires ongoing training and education for engineering and design teams. Providing resources, courses, and case studies that highlight successful DFM practices is crucial. Hands-on learning experiences, such as collaborative projects, practical design reviews, interactive workshops, and visits to manufacturing plants, can significantly enhance understanding and application of DFM principles.
3. Enhancing Outcomes Through Multidisciplinary Collaboration
Successful product development hinges on effective collaboration between design and production teams. The Tesla Model S serves as a prime example of what can be achieved through multidisciplinary collaboration. By integrating engineering, design, and production specialists, Tesla maximized the efficiency of assembly processes. This enhanced efficiency touched every part of the manufacturing process, leveraging advanced technologies such as aluminum casting and robotic assembly.
Integrating Design for Assembly (DFA) concepts into DFM represents another significant development. DFA aims to simplify product assembly by standardizing components, reducing part counts, and ensuring easy handling and alignment during assembly. Companies like Toyota utilize DFA methods to streamline assembly processes, reduce labor costs, and improve product quality. This integration of DFA with DFM underscores the importance of considering assembly efficiency during the design phase.
4. Leveraging Advanced DFM Techniques and Technologies
Advancements in DFM techniques and technologies have revolutionized manufacturing processes. Engineering software such as Siemens NX and CATIA from Dassault Systèmes allows for the simulation of machining, casting, and shaping, enabling engineers to identify potential problems early on. Simulation and virtual reality technologies also provide clients and internal teams with a comprehensive view of facility layouts, resource needs, and process flow, facilitating proactive adjustments.
The use of simulation and analysis tools continues to reshape the industrial landscape. These technologies reduce the time from design to production and lower manufacturing costs. Analysis and simulation tools can be used to examine multiple facets of manufacturing and design processes, including layout, system constraints, production changes, system performance, and labor.
Some top reasons to incorporate simulation into your DFM mindset include:
- Streamlined Performance: Enhance system performance with decision-support and training.
- Complex Variable Handling: Manage intricate interdependent variables and dynamics.
- Enhanced Comprehension: Improve system comprehension through detailed analysis.
- Advanced Assessments: Enable comprehensive “what if” assessments.
Process simulation tools mimic machining, casting, and forming operations, aiding in problem identification and parameter optimization for effective production. These tools help engineers optimize designs, anticipate performance, and evaluate manufacturability. Finite Element Analysis (FEA) is a powerful method for optimizing materials and reducing weight, while Computational Fluid Dynamics (CFD) evaluates fluid flow and heat transfer to develop better cooling systems and fluid-based manufacturing processes. Moldflow Analysis optimizes component design and mold setup for injection molding, reducing cycle times and errors.
Tool | Features | Benefits |
---|---|---|
Process Simulation | Simulates various production steps, including turning, casting, and shaping. | Identifies potential problems, adjusts process parameters (e.g., feed rates and cutting speeds), and enhances process efficiency. |
Discrete Event Simulation | Models complex processes and systems using discrete occurrences (e.g., logistics in a supply chain). | Boosts efficiency by maximizing resource utilization and eliminating inefficiencies. |
Design of Experiments (DOE) | Methodically plans trials to examine and enhance various factors. | Determines key factors for production processes, finds optimal process parameters, and reduces costly experiments. |
Failure Mode and Effect Analysis | Systematically assesses probable failure mechanisms for components or processes. | Determines pressing threats, ranks them by severity, and takes preventive action to minimize downtime, increase safety, and improve dependability. |
Digital Twin Simulation | Creates a digital copy, or “twin,” of an actual item or process. | Allows for predictive maintenance, performance optimization, scenario testing, and real-time monitoring without impacting actual operations. |
Statistical Process Control | Uses statistical approaches to oversee and manage production operations. | Helps identify outliers, maintains stable operations, boosts product quality, and reduces waste by keeping processes within specified parameters. |
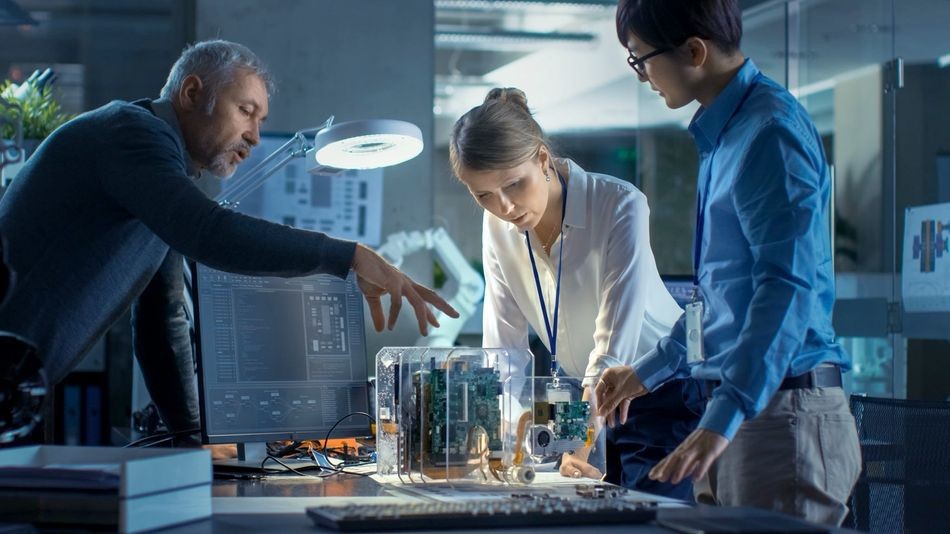
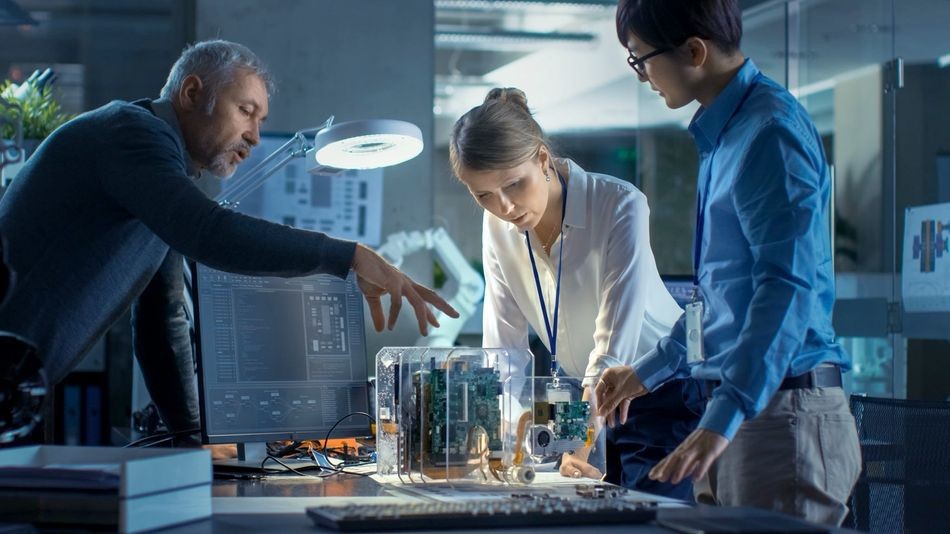
5. Revolutionizing DFM with Additive Manufacturing
3D printing and Additive Manufacturing (AM) continue to transform manufacturing in numerous ways, offering versatile designs, reduced material waste, and significant time and cost savings [3]. AM enables the creation of previously inconceivable, elaborate, and intricate geometries by building items layer by layer.
The ability to generate complex textures, patterns, and geometries is one of the many design freedoms made possible by additive manufacturing. AM can merge dozens of separate components into one, condensing assembly into a single step. Aerojet Rocketdyne, for example, saved 75% on production time and costs by using 3D-printed heat exchangers while simultaneously increasing their endurance and strength [4].
In medicine, 3D printing has had a substantial impact, enabling the creation of artificial skin for burn patients and expediting pharmaceutical development. 3D-printed models mimic the anatomy, size, texture, and color of real organs, tissues, and lesions, aiding in surgical preparation.
6. Optimizing Material Selection and Processes in DFM
Material selection significantly impacts DFM outcomes, as different materials possess distinct qualities that are critical during design and production. Carbon Fiber-Reinforced Polymers (CFRP) and other lightweight, high-strength composite materials have numerous potential applications in aircraft, improving structural integrity, reducing weight, and enhancing fuel economy.
Methods for cutting costs via material selection include life cycle cost analysis, value engineering, material substitution, bulk purchasing and negotiation, standardization, waste reduction and recycling, local sourcing, design optimization, technology and innovation, and regulatory and environmental considerations [5].
Technical issues and trade-offs, such as cost, performance, lead time, and scalability, come into play when choosing materials and processes for DFM. Opting for a straightforward manufacturing technique like injection molding, rather than CNC machining, can reduce production costs but may limit design flexibility. To maximize DFM results and balance design needs with production constraints, engineers must consider these trade-offs. A comprehensive strategy combining material science, industrial knowledge, and design optimization throughout the design phase is key to successful DFM methodology deployment.
7. Real-World Application of DFM in Engineering Projects
Case studies offer valuable insights into the benefits of DFM, allowing comparisons with competitors, learning from industry leaders’ mistakes, and generating ideas for your projects.
-
Case Study 1: Automotive Industry
A study aimed to make diesel engines more economically viable by reducing manufacturing and assembly costs [6]. The design study revealed opportunities to alter the production process, resulting in a 0.26% savings in the cylinder block and a 0.13% drop in the cost of structural and sealing subsystems. Eliminating unnecessary milling and non-pass bores, along with redundant painting, contributed to these cost reductions.
-
Case Study 2: Consumer Electronics
This case study highlights the importance of design in manufacturing for improving electronics manufacturing efficiency and component design. The customer faced challenges with flatness and ejection problems during molding. DFM analysis identified key areas for improvement, optimizing gear teeth arrangement and reducing rib features to streamline component design. These adjustments improved ejection and reduced material use, cost, and overall component weight.
8. Addressing Challenges and Considerations in DFM Implementation
Common challenges in implementing DFM methodology include a lack of cross-disciplinary teamwork, limitations imposed by current manufacturing capabilities, and a reluctance to deviate from traditional design approaches. Minimizing costs, making efficient use of materials, and balancing design goals with manufacturing constraints also pose significant obstacles.
To overcome these challenges:
- Maintain Balance: Balance material machinability and formability with strength, cost, and availability.
- Simplify Parts: Reduce part complexity to ease assembly and boost production efficiency.
- Align Design Tolerances: Ensure items fulfill functional requirements by aligning design tolerances with production capabilities.
- Proactive Analysis: Prioritize early-stage design analysis to address manufacturability concerns proactively.
- Promote Cooperation: Foster cross-functional cooperation.
- Use Simulation: Utilize sophisticated simulation technologies.
- Cultivate Culture: Cultivate a culture that appreciates DFM principles.
Key considerations for successful DFM implementation include using DFM concepts early in the design process, fostering multidisciplinary teams, assessing manufacturability with simulation and analytical tools, improving cost-effectiveness and performance, minimizing complexity, adhering to production limits, iteratively refining designs, and prioritizing continuous improvement.
9. Balancing Design Innovation with Manufacturing Constraints
The trade-off between design complexity and manufacturability is a real concern in innovative products. It is important to avoid sacrificing aesthetics or utility in favor of convenience of manufacture. Innovative materials can boost product performance but may also be hard to source or expensive.
Here are some ways to find a balance between innovation and manufacturing:
- Collaborate Early: Involve manufacturing specialists from the outset to help spot production limits.
- Use Iterative Prototyping: Test and improve designs with input from manufacturing trials to optimize them for production.
10. Ensuring Effective Communication and Knowledge Transfer
When using DFM principles, documentation and standardization are paramount for promoting knowledge transfer and ensuring good communication between design and production teams. Enhanced documentation allows for information sharing across different teams and project stages, reducing misunderstandings and guaranteeing uniformity in design and manufacturing procedures.
Tips for improving teamwork include:
- Form Interdisciplinary Teams: Include specialists from design, engineering, production, and quality assurance.
- Hold Regular Meetings: Provide updates and use collaborative technologies to ensure open and regular communication.
11. DFM and Industry 4.0 Integration
Combining DFM with cutting-edge technologies opens promising avenues for improving manufacturing processes and products. Industrial equipment can transmit data in real-time through Internet of Things (IoT) devices, revealing information about production efficiency and manufacturability issues. Artificial intelligence (AI) and machine learning (ML) algorithms can examine huge amounts of information provided by IoT sensors to automate decision-making, optimize process parameters, and forecast industrial outcomes.
DFM and the integration of Industry 4.0 technologies allow for automated decision-making, real-time monitoring, and predictive analytics in industrial processes.
DFM 4.0 offers many advantages:
- Better Product Quality: Enhanced quality through optimized processes.
- Efficient Manufacturing: Streamlined manufacturing for reduced costs.
- Reduced Downtime: Predictive maintenance minimizes downtime.
- Quick Reaction: Faster response to fluctuating market needs.
Conclusion: Embracing DFM for Engineering Excellence
DFM improves production results and encourages teamwork between design and manufacturing departments by facilitating the exchange of information and ideas. Working together shortens the time it takes to build a product, cuts down on mistakes, and simplifies the design process.
The IoT, AI, and ML are propelling DFM into the future, bringing about Industry 4.0 practices. These innovations enable automated decision-making, real-time monitoring, and predictive analytics, further enhancing product quality and the ability to meet customer requests.
By further integrating DFM with Industry 4.0 technology, transformations in manufacturing processes will continue. We will achieve more sustainable, efficient, and agile engineering methods in the future. At CONDUCT.EDU.VN, we are committed to providing the latest insights and best practices to ensure your DFM strategies are successful.
Need More Guidance?
Navigating the complexities of DFM can be challenging, but with the right knowledge and resources, you can achieve manufacturing success. At CONDUCT.EDU.VN, we offer detailed guides, practical examples, and expert advice to help you implement effective DFM strategies.
If you’re facing difficulties in finding reliable guidelines for specific situations or are unsure how to apply ethical principles in your organization, we’re here to help.
Visit CONDUCT.EDU.VN today to explore our comprehensive resources and discover how we can support your journey toward ethical excellence. Contact us at 100 Ethics Plaza, Guideline City, CA 90210, United States, or reach out via WhatsApp at +1 (707) 555-1234. Let conduct.edu.vn be your trusted partner in building a more ethical and successful future.
Frequently Asked Questions
-
Will a softer material always work better?
Yes, softer materials usually work better, allowing for greater control over cutting speed and depth, which reduces processing time.
-
How does DFM affect product quality?
DFM effects can improve product quality through simplified design, optimized material selection, improved assembly processes, reduction of manufacturing variabilities, and enhanced testing and validation.
-
What are the best tools to use for DFM?
Successful DFM implementation relies on computer-aided design software, design analysis software, finite element analysis software, DFM software modules, simulation tools, and collaboration platforms.
-
Will I save money with DFM practices?
Using DFM principles can result in substantial cost reductions throughout a product’s lifetime, including reduced material waste, lower production costs, fewer reworks, improved quality, and optimized tooling.
-
What is the most important part of DFM?
Incorporating DFM early in the product development phase is crucial for aligning design choices with production capabilities and restrictions, reducing the possibility of expensive adjustments later on.
-
How can DFM help reduce waste in manufacturing?
DFM minimizes waste by optimizing material usage, streamlining processes, and reducing errors, leading to more efficient and sustainable production. -
What role does simulation play in DFM?
Simulation tools play a vital role in DFM by allowing engineers to virtually test and optimize designs, identify potential issues, and improve manufacturability before physical production begins. -
Can DFM principles be applied to small-scale manufacturing operations?
Yes, DFM principles are scalable and can be applied to manufacturing operations of any size. Small-scale operations can benefit from improved efficiency, reduced costs, and higher product quality. -
How does DFM contribute to faster time-to-market?
DFM streamlines the product development process, reducing design iterations and production bottlenecks, which results in faster time-to-market. -
What are the key performance indicators (KPIs) to measure the success of a DFM implementation?
Key performance indicators include reduction in manufacturing costs, improvement in product quality, reduction in time-to-market, and increase in overall manufacturing efficiency.
References
[1] Siemens. Early DFM is more important than ever. Link
[2] Pacific-Research. Why DFM is important. Link
[3] Fictiv. 3D printing in aerospace. Link
[4] Additivemanufacturing. Aerojet Rocketdyne saved 75% on production time using 3D printed heat exchangers. Link
[5] Ncbi. Cost cutting methods via material selection. Link
[6] Slideshare. DFMA with Case Study -Diesel Engine Cost Reduction. Link
[7] Researchgate. Cross-disciplinary in collaborative design case study. Link