A Guide To Measuring Health And Safety Performance is crucial for fostering a safe and productive work environment. At CONDUCT.EDU.VN, we understand the importance of using both leading and lagging indicators to get a comprehensive view of your organization’s safety efforts, enabling you to enhance safety protocols and reduce workplace incidents. Explore practical strategies and tools for effective workplace safety measurement and build a culture of safety with our expert guidance.
1. Understanding the Importance of Health and Safety Performance Measurement
Measuring health and safety performance is essential for any organization committed to creating a safe and healthy workplace. It allows businesses to identify hazards, assess the effectiveness of safety programs, and continuously improve their safety practices. By proactively monitoring key performance indicators (KPIs), companies can minimize risks, prevent accidents, and foster a culture of safety.
1.1. Why Measure Health and Safety Performance?
- Risk Reduction: Identifying and mitigating potential hazards before they lead to incidents.
- Compliance: Ensuring adherence to regulatory requirements and industry standards.
- Continuous Improvement: Regularly evaluating and refining safety programs to enhance their effectiveness.
- Employee Engagement: Demonstrating a commitment to employee well-being, which can boost morale and productivity.
- Cost Savings: Reducing expenses associated with accidents, such as workers’ compensation claims and lost productivity.
1.2. Benefits of Effective Measurement
- Proactive Prevention: Moving beyond reactive measures to anticipate and prevent incidents.
- Data-Driven Decision Making: Using objective data to inform safety strategies and resource allocation.
- Improved Safety Culture: Cultivating a workplace where safety is a core value and everyone is accountable.
- Enhanced Reputation: Building trust with stakeholders through a demonstrated commitment to safety.
2. Key Performance Indicators (KPIs) for Health and Safety
Key Performance Indicators (KPIs) are measurable values that organizations use to track and evaluate the success of their health and safety efforts. These indicators provide insights into the effectiveness of safety programs and help identify areas for improvement. KPIs are typically divided into two main categories: lagging indicators and leading indicators.
2.1. Lagging Indicators
Lagging indicators are reactive metrics that measure the outcomes of past safety performance. While they provide valuable information, they reflect events that have already occurred and offer limited insight into preventing future incidents.
- Incident Rate: The number of incidents per a set number of working hours (e.g., per 100 full-time employees).
- Injury Frequency Rate (IFR): The number of recordable injuries per million hours worked.
- Injury Severity Rate (ISR): The number of days lost due to injuries per million hours worked.
- Workers’ Compensation Costs: The total cost of workers’ compensation claims, including medical expenses and lost wages.
- Lost Time Incident Frequency Rate (LTIFR): Number of lost time incidents per million hours worked.
2.2. Leading Indicators
Leading indicators are proactive metrics that measure the activities and conditions that prevent incidents from occurring. They provide insights into the effectiveness of safety management systems and help identify areas where preventive actions can be taken.
- Safety Training Hours: The total number of hours employees spend on safety training programs.
- Safety Audits and Inspections: The number and quality of safety audits and inspections conducted.
- Hazard Identification and Correction: The number of hazards identified and corrected.
- Employee Participation in Safety Programs: The level of employee involvement in safety committees and initiatives.
- Near Miss Reporting: The number of near misses reported, indicating a proactive safety culture.
3. Developing a Health and Safety Measurement System
Creating an effective health and safety measurement system involves several key steps, from defining objectives to implementing data collection processes and analyzing results. A well-designed system will provide valuable insights into your organization’s safety performance and guide continuous improvement efforts.
3.1. Define Objectives
- Identify Goals: Clearly define the objectives of your health and safety program. What do you want to achieve?
- Set Targets: Establish specific, measurable, achievable, relevant, and time-bound (SMART) targets for each KPI.
3.2. Select KPIs
- Choose Relevant Indicators: Select KPIs that align with your objectives and provide meaningful insights into your safety performance.
- Balance Leading and Lagging Indicators: Use a combination of both types of indicators to get a comprehensive view of your safety efforts.
3.3. Establish Data Collection Processes
- Determine Data Sources: Identify where you will collect data for each KPI (e.g., incident reports, training records, inspection reports).
- Implement Data Collection Procedures: Develop clear procedures for collecting and recording data accurately and consistently.
- Utilize Technology: Use software and digital tools to streamline data collection and analysis.
3.4. Analyze and Interpret Data
- Regular Analysis: Analyze data regularly to identify trends, patterns, and areas for improvement.
- Benchmarking: Compare your performance against industry benchmarks and best practices.
- Root Cause Analysis: Investigate the underlying causes of incidents and identify preventive measures.
3.5. Communicate Results
- Share Findings: Communicate the results of your analysis to stakeholders, including employees, management, and regulatory agencies.
- Transparency: Be transparent about your safety performance and areas for improvement.
3.6. Take Corrective Actions
- Implement Improvements: Develop and implement corrective actions to address identified deficiencies.
- Monitor Progress: Track the effectiveness of your corrective actions and make adjustments as needed.
- Continuous Improvement: Regularly review and refine your safety program to ensure it remains effective and relevant.
4. Leading Indicators in Detail
Leading indicators are proactive measures that provide insight into the effectiveness of safety management systems. They focus on activities and conditions that prevent incidents from occurring, allowing organizations to take preventive actions and improve their overall safety performance.
4.1. Types of Leading Indicators
- Activity-Based Indicators: Measure the frequency and quality of safety-related activities.
- Safety Training: Number of training sessions conducted, employee participation rates, and training effectiveness scores.
- Safety Audits and Inspections: Number of audits conducted, findings identified, and corrective actions implemented.
- Safety Meetings: Frequency of meetings, attendance rates, and topics discussed.
- Condition-Based Indicators: Assess the presence and effectiveness of safety controls and conditions.
- Hazard Identification: Number of hazards identified, risk assessments conducted, and control measures implemented.
- Equipment Maintenance: Frequency of equipment inspections, maintenance schedules followed, and repairs completed.
- Ergonomic Assessments: Number of ergonomic assessments conducted and recommendations implemented.
- Perception-Based Indicators: Gauge employee attitudes and perceptions about safety.
- Safety Culture Surveys: Employee responses to surveys assessing safety attitudes, beliefs, and behaviors.
- Focus Groups: Feedback from focus groups on safety issues and concerns.
- Suggestion Programs: Number of safety suggestions submitted and implemented.
4.2. Examples of Leading Indicators in Practice
Leading Indicator | Description | Measurement |
---|---|---|
Safety Training Completion Rate | Percentage of employees who have completed required safety training. | (Number of employees who completed training / Total number of employees required to complete training) x 100 |
Hazard Identification Rate | Number of hazards identified per month. | Total number of hazards identified each month. |
Corrective Action Completion | Percentage of corrective actions completed within the specified timeframe. | (Number of corrective actions completed on time / Total number of corrective actions required) x 100 |
Safety Audit Frequency | Number of safety audits conducted per quarter. | Total number of safety audits conducted each quarter. |
Near Miss Reporting Rate | Number of near misses reported per month. | Total number of near misses reported each month. |
Employee Participation Rate | Percentage of employees participating in safety committees or safety-related activities. | (Number of employees participating in safety activities / Total number of employees) x 100 |
Safety Observation Rate | Number of safety observations conducted per month. | Total number of safety observations conducted each month. |
Preventative Maintenance Rate | Percentage of preventative maintenance tasks completed on time. | (Number of preventative maintenance tasks completed on time / Total number of preventative maintenance tasks scheduled) x 100 |
Safety Communication Frequency | Number of safety communications (e.g., newsletters, emails) sent to employees per month. | Total number of safety communications sent each month. |
Safety Suggestion Rate | Number of safety suggestions submitted by employees per month. | Total number of safety suggestions submitted each month. |
Ergonomic Assessment Rate | Number of ergonomic assessments completed per quarter. | Total number of ergonomic assessments completed each quarter. |
Compliance Rate | Percentage of compliance tasks (e.g., inspections, certifications) completed on time. | (Number of compliance tasks completed on time / Total number of compliance tasks required) x 100 |
Safety Leadership Visibility | Number of safety walk-arounds or engagements by leadership per month. | Total number of safety walk-arounds or engagements by leadership each month. |
Safety Task Analysis Rate | Number of safety task analyses completed per year. | Total number of safety task analyses completed each year. |
Training Effectiveness Score | Average score on post-training assessments. | Average score of employee post-training assessments. |
Job Safety Analysis (JSA) Rate | Number of JSAs conducted for high-risk tasks per year. | Total number of JSAs conducted for high-risk tasks each year. |
Safety Climate Score | Average score from employee safety climate surveys. | Average score of employee responses from safety climate surveys. |
Permit-to-Work (PTW) Rate | Number of PTWs issued and followed per month for hazardous activities. | Total number of PTWs issued and followed each month for hazardous activities. |
Behavior-Based Safety (BBS) | Number of safe behaviors observed and documented per month. | Total number of safe behaviors observed and documented each month. |
Critical Control Monitoring | Number of critical controls verified and validated per month. | Total number of critical controls verified and validated each month. |
Proactive Hazard Closure Rate | Number of proactive hazards closed out before an incident occurs. | Total number of proactive hazards closed out before an incident occurs. |
Safety Equipment Usage Rate | Percentage of employees using required safety equipment during specific tasks. | (Number of employees using required safety equipment / Total number of employees performing the task) x 100 |
Management Commitment Index | Average score from employee surveys on management commitment to safety. | Average score of employee responses from surveys evaluating management commitment to safety. |
Emergency Drill Completion Rate | Percentage of emergency drills completed as per schedule. | (Number of emergency drills completed as scheduled / Total number of emergency drills scheduled) x 100 |
Policy Review Rate | Number of safety policies reviewed and updated per year. | Total number of safety policies reviewed and updated each year. |
Safety Resources Availability | Percentage of required safety resources (e.g., PPE, first aid) readily available when needed. | (Number of times safety resources were available when needed / Total number of times safety resources were needed) x 100 |
Housekeeping Audit Rate | Number of housekeeping audits completed per month. | Total number of housekeeping audits completed each month. |
Ergonomic Improvement Project | Number of ergonomic improvement projects initiated and completed per year. | Total number of ergonomic improvement projects initiated and completed each year. |
Machine Guarding Compliance | Percentage of machinery with compliant guarding in place. | (Number of machinery with compliant guarding / Total number of machinery) x 100 |
Chemical Safety Audits | Number of chemical safety audits conducted per year. | Total number of chemical safety audits conducted each year. |
Contractor Safety Performance | Score based on contractor safety performance metrics. | Calculated based on a scoring system evaluating contractor safety performance metrics. |
Incident Investigation Quality | Score based on the quality and thoroughness of incident investigations. | Calculated based on a scoring system evaluating the quality and thoroughness of incident investigations. |
Remote Worker Safety Checks | Number of remote worker safety checks completed per quarter. | Total number of remote worker safety checks completed each quarter. |
Emergency Preparedness Drills | Number of emergency preparedness drills (e.g., fire, evacuation) conducted per year. | Total number of emergency preparedness drills conducted each year. |



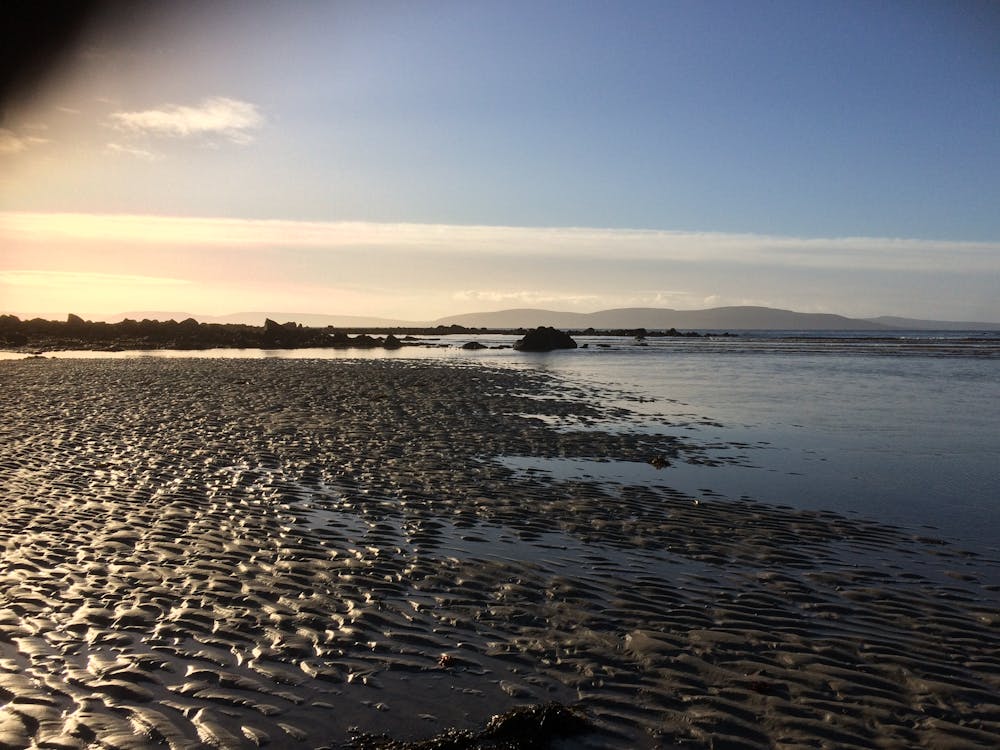
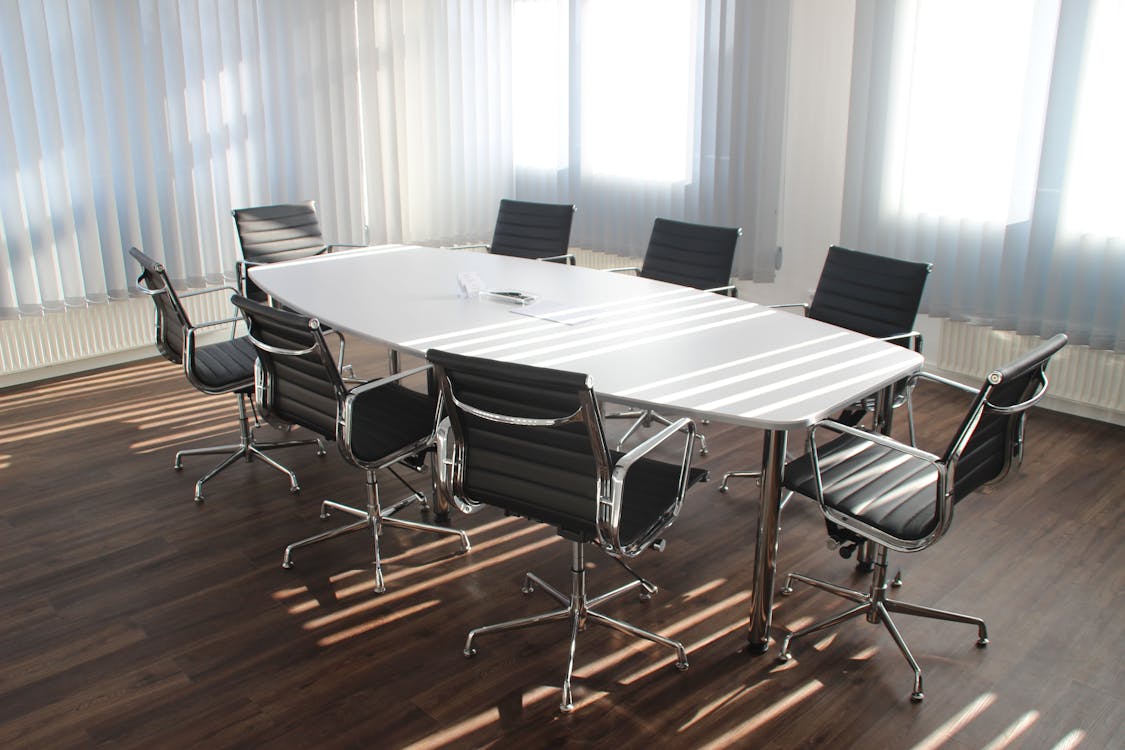
4.3. Implementing Leading Indicators
- Identify Critical Activities: Determine the activities that have the greatest impact on safety performance.
- Develop Measurement Methods: Create clear and consistent methods for measuring leading indicators.
- Set Targets: Establish realistic and achievable targets for each indicator.
- Monitor and Track: Regularly monitor and track progress towards targets.
- Provide Feedback: Share results with employees and provide feedback on their performance.
- Recognize Success: Recognize and reward employees for their contributions to safety.
5. Lagging Indicators in Detail
Lagging indicators are reactive measures that reflect past safety performance. They provide valuable information about the outcomes of safety efforts but offer limited insight into preventing future incidents.
5.1. Types of Lagging Indicators
- Incident Rate: Measures the number of incidents per a set number of working hours.
- Calculation: (Number of incidents / Total hours worked) x a constant (e.g., 200,000 for 100 full-time employees)
Note: This constant may vary depending on your industry and the standards you are using.
- Calculation: (Number of incidents / Total hours worked) x a constant (e.g., 200,000 for 100 full-time employees)
- Injury Frequency Rate (IFR): Measures the number of recordable injuries per million hours worked.
- Calculation: (Number of recordable injuries / Total hours worked) x 1,000,000
- Injury Severity Rate (ISR): Measures the number of days lost due to injuries per million hours worked.
- Calculation: (Number of days lost due to injuries / Total hours worked) x 1,000,000
- Workers’ Compensation Costs: Measures the total cost of workers’ compensation claims.
- Components: Medical expenses, lost wages, and legal fees.
- Lost Time Incident Frequency Rate (LTIFR): Number of lost time incidents per million hours worked.
- Calculation: (Number of lost time incidents / Total hours worked) x 1,000,000
5.2. Analyzing Lagging Indicators
- Track Trends: Monitor lagging indicators over time to identify trends and patterns.
- Compare to Benchmarks: Compare your performance against industry benchmarks and best practices.
- Identify Root Causes: Investigate the underlying causes of incidents to identify preventive measures.
- Use Data to Inform Decisions: Use lagging indicator data to inform safety strategies and resource allocation.
5.3. Limitations of Lagging Indicators
- Reactive: They only reflect past performance and provide limited insight into preventing future incidents.
- Limited Information: They provide little information about the underlying causes of incidents.
- Potential for Underreporting: Incidents may go unreported, leading to inaccurate data.
6. Integrating Leading and Lagging Indicators
Integrating leading and lagging indicators provides a comprehensive view of your organization’s safety performance. By combining proactive and reactive measures, you can identify both the strengths and weaknesses of your safety program and take targeted actions to improve safety outcomes.
6.1. How to Integrate
- Establish a Balanced Scorecard: Create a balanced scorecard that includes both leading and lagging indicators.
- Monitor and Analyze Data: Regularly monitor and analyze data from both types of indicators.
- Identify Correlations: Look for correlations between leading and lagging indicators to understand how preventive activities impact safety outcomes.
- Use Data to Drive Improvements: Use the data to inform safety strategies and resource allocation.
6.2. Example of Integration
Leading Indicator | Lagging Indicator | Correlation |
---|---|---|
Increased Safety Training Hours | Decreased Incident Rate | Increased training leads to better awareness and safer practices, resulting in fewer incidents. |
More Frequent Safety Audits | Reduced Injury Frequency | Regular audits identify and correct hazards, reducing the likelihood of injuries. |
Higher Near Miss Reporting Rate | Lower Workers’ Comp Costs | Encouraging near miss reporting allows for preventive actions, reducing the severity and frequency of incidents, which lowers workers’ compensation costs. |
Improved Hazard Identification | Fewer Lost Time Incidents | Identifying and correcting hazards proactively prevents incidents that lead to lost time. |
Increased Employee Participation | Enhanced Safety Culture | Engaging employees in safety programs fosters a culture of safety, leading to safer behaviors and better overall safety performance. |
Completion of Ergonomic Assessments | Reduction in Musculoskeletal | Targeted assessments and implementation of ergonomic interventions reduces number of musculoskeletal disorders. |
7. Case Studies: Successful Implementation of Health and Safety Measurement
Examining real-world case studies can provide valuable insights into how organizations have successfully implemented health and safety measurement systems. These examples demonstrate the practical application of KPIs and the benefits of a proactive approach to safety.
7.1. Case Study 1: Manufacturing Company
- Challenge: High incident rate and increasing workers’ compensation costs.
- Solution: Implemented a comprehensive health and safety measurement system, including:
- Leading Indicators: Increased safety training hours, more frequent safety audits, and improved hazard identification.
- Lagging Indicators: Tracked incident rate, injury frequency rate, and workers’ compensation costs.
- Results:
- Incident rate decreased by 40%.
- Workers’ compensation costs reduced by 25%.
- Improved employee morale and productivity.
7.2. Case Study 2: Construction Company
- Challenge: Frequent near misses and safety violations.
- Solution: Focused on improving safety culture and employee engagement by:
- Leading Indicators: Increased near miss reporting rate, more frequent safety meetings, and improved communication.
- Lagging Indicators: Tracked incident rate, lost time incident frequency rate, and number of safety violations.
- Results:
- Near miss reporting rate increased by 50%.
- Incident rate decreased by 30%.
- Safety violations reduced by 60%.
7.3. Case Study 3: Healthcare Organization
- Challenge: High rates of employee burnout and potential safety risks due to long hours and stressful conditions.
- Solution: Implemented a health and well-being program with specific metrics for safety and employee health:
- Leading Indicators:
- Employee Participation in Wellness Programs: Tracked the percentage of employees participating in stress management, ergonomic training, and health check-ups.
- Safety Training Completion Rate: Monitored completion of training modules on infection control, patient handling, and emergency response.
- Hazard Reporting Rate: Measured the number of safety hazards reported by employees per month.
- Lagging Indicators:
- Employee Injury Rate: Tracked the number of workplace injuries (e.g., slips, falls, needle-stick injuries) per 100 full-time employees.
- Employee Burnout Rate: Measured through periodic surveys assessing emotional exhaustion and cynicism.
- Patient Safety Incidents: Monitored incidents like medication errors, patient falls, and hospital-acquired infections.
- Results:
- Increased participation in wellness programs by 60% within the first year.
- Reduced employee injury rate by 25% over two years.
- Decrease in reported burnout among staff by 20%.
- Improved patient safety metrics, with a 15% reduction in medication errors.
- Leading Indicators:
8. The Role of Technology in Health and Safety Measurement
Technology plays a critical role in streamlining health and safety measurement processes, improving data accuracy, and enhancing the overall effectiveness of safety programs. From software solutions to wearable devices, technology offers a range of tools to support proactive safety management.
8.1. Types of Technology Solutions
- Safety Management Software: Centralized platforms for managing safety data, tracking KPIs, and generating reports.
- Mobile Apps: Tools for conducting inspections, reporting hazards, and accessing safety information on the go.
- Wearable Devices: Sensors and devices that monitor employee health and safety in real-time.
- Data Analytics Tools: Software for analyzing safety data, identifying trends, and predicting potential incidents.
- IoT (Internet of Things) Devices: Connected devices that monitor environmental conditions and equipment performance.
- Examples include air quality monitors, noise level sensors, and equipment vibration sensors.
8.2. Benefits of Using Technology
- Improved Data Accuracy: Automated data collection reduces the risk of human error.
- Real-Time Monitoring: Provides immediate insights into safety performance.
- Enhanced Reporting: Simplifies the process of generating reports and sharing data with stakeholders.
- Proactive Prevention: Enables proactive identification and mitigation of hazards.
- Increased Efficiency: Streamlines safety management processes, saving time and resources.
9. Common Challenges and How to Overcome Them
Implementing a health and safety measurement system can present several challenges, from resistance to change to difficulties in data collection and analysis. However, by anticipating these challenges and implementing proactive strategies, organizations can overcome them and achieve their safety goals.
9.1. Challenges
- Resistance to Change: Employees and management may resist new safety processes and procedures.
- Lack of Resources: Limited resources (e.g., time, budget, personnel) can hinder implementation efforts.
- Data Collection Difficulties: Inaccurate or incomplete data can compromise the effectiveness of the measurement system.
- Complexity: Complex safety programs and regulations can make it difficult to identify and track relevant KPIs.
- Lack of Buy-In: Without support from leadership and engagement from employees, safety initiatives may fail.
9.2. Solutions
- Communication and Training: Clearly communicate the benefits of the measurement system and provide comprehensive training to employees.
- Allocate Resources: Dedicate sufficient resources to support the implementation and maintenance of the system.
- Improve Data Collection Processes: Implement clear procedures for collecting and recording data, and use technology to automate the process.
- Simplify Processes: Streamline safety programs and regulations to make it easier to identify and track relevant KPIs.
- Foster a Safety Culture: Promote a culture of safety by engaging employees in safety programs and recognizing their contributions.
10. Regulatory Requirements and Standards
Adhering to regulatory requirements and industry standards is essential for ensuring a safe and compliant workplace. Understanding the relevant regulations and incorporating them into your health and safety measurement system can help you avoid penalties and protect your employees.
10.1. Key Regulations and Standards
- Occupational Safety and Health Administration (OSHA): Sets and enforces standards for workplace safety and health in the United States.
- European Agency for Safety and Health at Work (EU-OSHA): Provides information, guidance, and tools for improving workplace safety and health in Europe.
- International Organization for Standardization (ISO): Develops international standards for quality, safety, and environmental management.
- National Institute for Occupational Safety and Health (NIOSH): Conducts research and provides recommendations for preventing work-related injuries and illnesses.
- ANSI Standards: The American National Standards Institute (ANSI) oversees the creation, promulgation, and use of thousands of norms and guidelines that directly impact businesses in nearly every sector.
- State and Local Regulations: Many states and local jurisdictions have their own safety regulations that organizations must comply with.
10.2. Integrating Regulations into Your Measurement System
- Identify Applicable Regulations: Determine which regulations and standards apply to your industry and operations.
- Incorporate Requirements: Integrate the requirements of these regulations into your safety programs and measurement system.
- Monitor Compliance: Regularly monitor compliance with regulations and standards.
- Conduct Audits: Perform periodic audits to ensure that your safety programs are effective and compliant.
11. Building a Proactive Safety Culture
Creating a proactive safety culture is essential for achieving long-term improvements in health and safety performance. A proactive culture is one where safety is a core value, and everyone is accountable for preventing incidents and promoting a safe work environment.
11.1. Key Elements of a Proactive Safety Culture
- Leadership Commitment: Visible and active support from leadership.
- Employee Engagement: Active participation and involvement of employees in safety programs.
- Open Communication: Transparent and open communication about safety issues and concerns.
- Continuous Improvement: A commitment to continuously improving safety performance.
- Recognition and Rewards: Recognizing and rewarding employees for their contributions to safety.
- Training and Education: Comprehensive training and education programs for all employees.
- Accountability: Holding individuals accountable for their safety responsibilities.
11.2. Strategies for Building a Proactive Culture
- Leadership Involvement: Leaders should actively participate in safety activities, such as safety meetings and inspections.
- Employee Empowerment: Empower employees to identify hazards, report concerns, and suggest improvements.
- Training and Education: Provide comprehensive training and education programs for all employees.
- Recognition and Rewards: Recognize and reward employees for their contributions to safety.
- Communication: Communicate regularly about safety issues, performance, and improvements.
- Accountability: Hold individuals accountable for their safety responsibilities.
- Feedback Mechanisms: Implement feedback mechanisms to gather input from employees on safety issues.
12. Frequently Asked Questions (FAQs) About Measuring Health and Safety Performance
1. What is the difference between leading and lagging indicators?
- Leading indicators are proactive measures that predict future safety performance, while lagging indicators are reactive measures that reflect past safety performance.
2. Why is it important to measure health and safety performance?
- Measuring health and safety performance helps organizations identify hazards, assess the effectiveness of safety programs, and continuously improve safety practices.
3. How do I select the right KPIs for my organization?
- Select KPIs that align with your objectives, provide meaningful insights into your safety performance, and balance leading and lagging indicators.
4. What are some common challenges in implementing a health and safety measurement system?
- Common challenges include resistance to change, lack of resources, data collection difficulties, and complexity.
5. How can I overcome resistance to change?
- Communicate the benefits of the measurement system, provide comprehensive training, and involve employees in the process.
6. What role does technology play in health and safety measurement?
- Technology can streamline data collection, improve data accuracy, enhance reporting, and enable proactive prevention.
7. How can I build a proactive safety culture?
- Foster leadership commitment, employee engagement, open communication, continuous improvement, and recognition and rewards.
8. What regulatory requirements should I be aware of?
- Be aware of regulations from OSHA, EU-OSHA, ISO, NIOSH, and state and local agencies.
9. How often should I review and update my health and safety measurement system?
- Review and update your system regularly to ensure it remains effective and relevant.
10. Where can I find more information and resources on health and safety measurement?
- Visit websites like CONDUCT.EDU.VN, OSHA, EU-OSHA, and NIOSH for more information and resources.
13. Conclusion: Achieving Excellence in Health and Safety
Measuring health and safety performance is essential for creating a safe and healthy workplace. By implementing a comprehensive measurement system that includes both leading and lagging indicators, organizations can identify hazards, assess the effectiveness of safety programs, and continuously improve their safety practices. A proactive safety culture, supported by technology and driven by leadership commitment, is the key to achieving excellence in health and safety and ensuring the well-being of all employees.
Are you ready to elevate your organization’s health and safety performance? Visit CONDUCT.EDU.VN for detailed guides, resources, and expert advice on implementing effective measurement systems and building a proactive safety culture. Contact us at 100 Ethics Plaza, Guideline City, CA 90210, United States, or reach out via Whatsapp at +1 (707) 555-1234. Let conduct.edu.vn be your partner in creating a safer and healthier workplace for everyone.