Steam Turbine Technology: A Practical Guide available at CONDUCT.EDU.VN delivers crucial insights into optimizing steam turbine performance and longevity. This guide offers actionable strategies for maintenance, efficiency improvements, and innovative solutions, ensuring optimal operation and reliability, focusing on essential aspects like advanced sealing solutions, lubricant management, and contamination control, thus reducing downtime and enhancing overall system performance. Delve into the depths of steam turbine innovation and best practices for enhanced energy solutions.
1. Understanding Steam Turbine Technology
Steam turbines are vital components in power generation and various industrial processes, converting thermal energy into mechanical work. Their efficient and reliable operation is paramount for maximizing energy output and minimizing downtime. This practical guide delves into the core principles, components, and operational aspects of steam turbine technology.
1.1. The Basics of Steam Turbines
Steam turbines operate on the Rankine cycle, using high-pressure steam to rotate a series of blades connected to a rotor. As the steam expands and cools, it imparts energy to the blades, causing the rotor to spin and drive a generator or other mechanical equipment. The efficiency of a steam turbine depends on various factors, including steam temperature and pressure, turbine design, and operating conditions.
1.2. Key Components of a Steam Turbine
A steam turbine comprises several essential components:
- Nozzles: Direct high-pressure steam onto the turbine blades, converting thermal energy into kinetic energy.
- Blades: Convert the kinetic energy of the steam into mechanical energy, causing the rotor to rotate.
- Rotor: The rotating assembly that houses the blades and transmits the mechanical energy to the generator or other equipment.
- Casing: Encloses the turbine components, providing structural support and containing the steam.
- Bearings: Support the rotor and allow it to rotate smoothly with minimal friction.
- Seals: Prevent steam leakage and maintain pressure within the turbine.
- Control System: Regulates steam flow, turbine speed, and other operating parameters.
Understanding the function and interaction of these components is crucial for effective maintenance and troubleshooting.
1.3. Types of Steam Turbines
Steam turbines are classified based on several factors, including:
- Impulse Turbines: Utilize nozzles to convert steam pressure into velocity, directing high-speed steam onto the blades.
- Reaction Turbines: Employ both fixed and moving blades to expand the steam gradually, extracting energy through both pressure and velocity changes.
- Condensing Turbines: Exhaust steam into a condenser to create a vacuum, increasing the pressure differential and improving efficiency.
- Non-Condensing Turbines: Exhaust steam at a higher pressure for use in other processes, such as heating or industrial applications.
- Extraction Turbines: Allow for the extraction of steam at intermediate stages for various process requirements.
Each type of turbine has its advantages and is suited for specific applications based on energy requirements and operational constraints.
2. Lubrication and Bearing Protection in Steam Turbines
Proper lubrication is crucial for the reliable operation of steam turbines. Effective bearing protection is essential to prevent contamination and ensure the longevity of bearings, which are critical components in turbine functionality.
2.1. The Importance of Lubrication
Lubrication minimizes friction and wear between moving parts, dissipates heat, and protects against corrosion. In steam turbines, bearings are particularly vulnerable to wear and damage if not adequately lubricated. The lubricant forms a thin film between the bearing surfaces, preventing direct contact and reducing friction.
2.2. Types of Lubricants Used in Steam Turbines
Several types of lubricants are used in steam turbines, each with specific properties and applications:
- Mineral Oils: Widely used due to their excellent lubricating properties and cost-effectiveness. They provide good thermal stability and resistance to oxidation.
- Synthetic Oils: Offer superior performance at high temperatures and pressures. They also have better oxidation resistance and longer service life compared to mineral oils.
- Phosphate Esters: Used in applications where fire resistance is critical. They have excellent thermal stability and are compatible with various materials.
- Greases: Used in specific applications where oil lubrication is not feasible. They provide a protective layer and reduce friction in slow-moving components.
The selection of the appropriate lubricant depends on the turbine’s operating conditions, bearing type, and manufacturer’s recommendations.
2.3. Bearing Protection Techniques
Protecting bearings from contamination is essential for extending their service life and preventing failures. Common bearing protection techniques include:
- Sealing: Using seals to prevent the ingress of contaminants such as water, dust, and other particles into the bearing housing.
- Filtration: Installing filters to remove contaminants from the lubricant, ensuring that only clean oil reaches the bearings.
- Desiccation: Using desiccants to remove moisture from the air entering the bearing housing, preventing corrosion and lubricant degradation.
- Regular Oil Analysis: Monitoring the condition of the lubricant through regular oil analysis to detect contamination, wear, and other issues early on.
Implementing these techniques can significantly improve the reliability and longevity of steam turbine bearings.
Figure 2. Lip Seal (Top Portion) and Modern Rotating Labyrinth Seal (Lower Portion, also Enlargement on Right Side) 4
3. Advanced Sealing Solutions
Effective sealing solutions are crucial for preventing steam leakage and contamination in steam turbines. Modern bearing protector seals offer enhanced protection against water, steam, and airborne contaminants, improving turbine efficiency and reliability.
3.1. Types of Bearing Protector Seals
Several types of bearing protector seals are available, each with its advantages and applications:
- Lip Seals: Traditional seals that use a flexible lip to contact the rotating shaft, creating a barrier against contaminants. However, they are prone to wear and may not be suitable for high-speed applications.
- Labyrinth Seals: Non-contact seals that use a series of interlocking grooves to create a tortuous path for contaminants. They offer low friction and long service life but may not provide a perfect seal.
- Magnetic Seals: Use magnetic force to create a tight seal between the rotating and stationary components. They offer excellent sealing performance and are suitable for high-speed applications.
The selection of the appropriate seal depends on the turbine’s operating conditions, speed, and the level of protection required.
3.2. Rotating Labyrinth Seals
Rotating labyrinth seals are advanced sealing solutions that provide superior protection against contamination. They use a series of rotating and stationary components with interlocking grooves to create a complex path for contaminants, preventing their ingress into the bearing housing.
3.3. Magnetic Bearing Housing Seals
Magnetic bearing housing seals offer excellent sealing performance by using magnetic force to create a tight seal. They are particularly effective in preventing the ingress of water, steam, and other airborne contaminants, ensuring the longevity of bearings.
Figure 3a and 3b. Two Different Dual-face Magnetic Seal Styles 4 O-rings (2, 4, 6, 10), Snap Ring (11), Rotating Face (1), Stationary Faces (3, 9), Stationary Magnets (8), Magnet Carrier (7), and Outer Body (5).
4. Contamination Control
Contamination control is a critical aspect of steam turbine maintenance, as even small amounts of contaminants can significantly reduce bearing life and turbine efficiency. Effective contamination control strategies include preventing contaminant ingress, removing existing contaminants, and monitoring lubricant condition.
4.1. Sources of Contamination
Contaminants can enter steam turbines from various sources:
- Airborne Particles: Dust, dirt, and other particles can enter the turbine through vents, seals, and other openings.
- Water: Steam leakage, condensation, and water ingress can contaminate the lubricant and cause corrosion.
- Process Fluids: Leakage of process fluids into the turbine can contaminate the lubricant and damage components.
- Wear Debris: Wear particles from bearings, gears, and other components can accumulate in the lubricant and accelerate wear.
Identifying and addressing these sources of contamination is essential for effective contamination control.
4.2. Methods for Preventing Contamination
Several methods can be used to prevent contamination in steam turbines:
- Sealing: Using effective seals to prevent the ingress of contaminants into the turbine.
- Filtration: Installing filters to remove contaminants from the lubricant.
- Desiccation: Using desiccants to remove moisture from the air entering the turbine.
- Proper Maintenance Practices: Implementing proper maintenance practices, such as regular cleaning and inspection, to prevent contamination.
These methods help maintain the cleanliness of the lubricant and protect the turbine components from damage.
4.3. Removing Existing Contaminants
In addition to preventing contamination, it is also essential to remove existing contaminants from the lubricant. Common methods for removing contaminants include:
- Filtration: Using filters to remove solid particles from the lubricant.
- Centrifugation: Using centrifugal force to separate contaminants from the lubricant.
- Electrostatic Separation: Using electrostatic forces to remove contaminants from the lubricant.
- Chemical Treatment: Using chemical additives to neutralize contaminants and improve lubricant condition.
These methods help maintain the lubricant’s quality and extend its service life.
4.4. Monitoring Lubricant Condition
Regular monitoring of lubricant condition is essential for detecting contamination, wear, and other issues early on. Common methods for monitoring lubricant condition include:
Monitoring Method | Description | Benefits |
---|---|---|
Visual Inspection | Examining the lubricant for changes in color, clarity, and sediment. | Simple and inexpensive, provides a quick indication of lubricant condition. |
Viscosity Analysis | Measuring the lubricant’s viscosity to detect changes in its lubricating properties. | Indicates lubricant degradation, contamination, and wear. |
Acid Number Analysis | Measuring the lubricant’s acidity to detect oxidation and degradation. | Indicates the need for lubricant replacement or treatment. |
Wear Debris Analysis | Analyzing the lubricant for wear particles to identify potential component failures. | Provides valuable information about the condition of bearings, gears, and other components. |
Water Content Analysis | Measuring the lubricant’s water content to detect water contamination. | Indicates potential corrosion and lubricant degradation. |
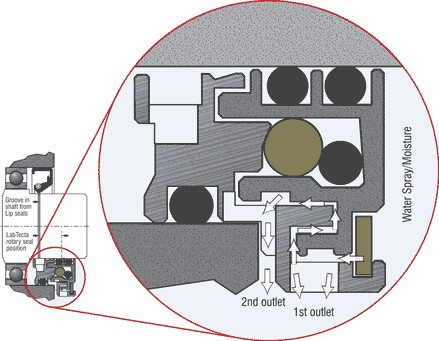
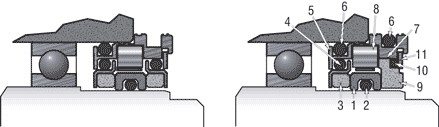
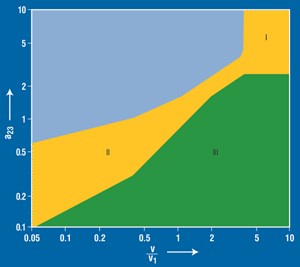
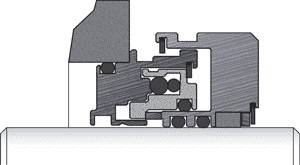
Regular oil analysis helps identify potential problems before they lead to costly failures.
5. Lube Oil Application Flaws and Their Impact
Flaws in lube oil application and contamination are major contributors to bearing failures in small steam turbines. Addressing these issues through proper maintenance and advanced sealing solutions can significantly improve turbine reliability and longevity.
5.1. Common Lube Oil Application Flaws
Several common flaws in lube oil application can lead to bearing failures:
- Insufficient Lubrication: Not providing enough lubricant to the bearings, leading to increased friction and wear.
- Improper Lubricant Selection: Using the wrong type of lubricant for the application, resulting in poor lubrication and accelerated wear.
- Contaminated Lubricant: Using contaminated lubricant, which can introduce abrasive particles and accelerate wear.
- Inadequate Filtration: Not filtering the lubricant properly, allowing contaminants to accumulate and cause damage.
- Infrequent Lubricant Changes: Not changing the lubricant frequently enough, allowing it to degrade and lose its lubricating properties.
Addressing these flaws through proper maintenance and lubrication practices is essential for preventing bearing failures.
5.2. The Impact of Contamination on Bearing Life
Contamination can significantly reduce bearing life in steam turbines. Even small amounts of contaminants can accelerate wear, increase friction, and cause premature failure. Studies have shown that the life of a bearing can be reduced by as much as 60% with as little as 100 ppm of dissolved water in the lube oil.
According to a study by FAG Bearings, lubricant contamination significantly impacts bearing life. The study indicates that even minor contamination levels can drastically reduce the operational lifespan of bearings. Specifically, they emphasize maintaining lubricant cleanliness to optimize bearing performance and longevity.
5.3. Cost-Effectiveness of Bearing Protection
Investing in bearing protection is a cost-effective way to improve steam turbine reliability and reduce maintenance costs. By preventing contamination and ensuring proper lubrication, bearing protection can significantly extend bearing life and reduce the risk of costly failures.
6. Viscosity and Bearing Life Adjustment
The viscosity of the lubricant plays a crucial role in bearing life. Maintaining the correct viscosity is essential for ensuring adequate lubrication and preventing wear.
6.1. The Importance of Viscosity
Viscosity is a measure of a fluid’s resistance to flow. In lubrication, viscosity is crucial for maintaining a sufficient oil film between bearing surfaces, preventing direct contact and reducing friction. The correct viscosity depends on the bearing type, operating conditions, and manufacturer’s recommendations.
6.2. Viscosity Ratio and Bearing Life Adjustment
The viscosity ratio (v/v1) is the ratio of the lubricant’s operating viscosity to its rated viscosity. This ratio is used to determine a bearing life adjustment factor, which indicates the impact of viscosity on bearing life. A viscosity ratio of less than 1 indicates that the lubricant’s viscosity is below the desired level, which can reduce bearing life.
6.3. Improving Bearing Life with Effective Sealing
Effective bearing protector seals can improve bearing life by maintaining lubricant viscosity and preventing contamination. By preventing the ingress of water, steam, and other contaminants, these seals help maintain the lubricant’s viscosity and prevent degradation.
Figure 1. Contamination Rolling Bearing Life Adjustment Factor a23 vs. Viscosity Ratio v/v1 Ref. 2
7. Lip Seals vs. Rotating Labyrinth Seals: A Comparison
Lip seals and rotating labyrinth seals are two common types of bearing protector seals. While lip seals have been used for many years, rotating labyrinth seals offer superior performance in high-speed applications and provide better protection against contamination.
7.1. Lip Seals: Advantages and Disadvantages
Lip seals are simple and inexpensive seals that use a flexible lip to contact the rotating shaft. They are effective in low-speed applications and provide a good barrier against contaminants. However, they are prone to wear and may not be suitable for high-speed applications.
7.2. Rotating Labyrinth Seals: Advantages and Disadvantages
Rotating labyrinth seals are non-contact seals that use a series of interlocking grooves to create a tortuous path for contaminants. They offer low friction and long service life but may not provide a perfect seal. They are suitable for high-speed applications and provide better protection against contamination compared to lip seals.
7.3. Choosing the Right Seal for Your Application
The choice between lip seals and rotating labyrinth seals depends on the turbine’s operating conditions, speed, and the level of protection required. For high-speed applications and environments with high levels of contamination, rotating labyrinth seals are the preferred choice.
8. Practical Steps for Implementing Advanced Sealing Solutions
Implementing advanced sealing solutions involves several practical steps:
- Assess the Turbine’s Operating Conditions: Determine the turbine’s operating speed, temperature, and the level of contamination in the environment.
- Select the Appropriate Seal: Choose the appropriate seal based on the turbine’s operating conditions and the level of protection required.
- Install the Seal Properly: Follow the manufacturer’s instructions for installing the seal correctly.
- Monitor Seal Performance: Regularly monitor the seal’s performance to ensure that it is functioning properly.
- Maintain the Seal: Perform regular maintenance on the seal to ensure its longevity and effectiveness.
By following these steps, you can effectively implement advanced sealing solutions and improve the reliability of your steam turbines.
Figure 4. This Variant of Figure 2 Incorporates Considerable Axial Float Capability and is Used on Small Steam Turbines
9. Case Studies: Success Stories in Steam Turbine Technology
Several case studies demonstrate the effectiveness of advanced sealing solutions and contamination control strategies in improving steam turbine reliability.
9.1. Case Study 1: Reducing Bearing Failures in a Power Plant
A power plant implemented advanced sealing solutions and improved lubrication practices in its steam turbines. As a result, bearing failures were reduced by 50%, and turbine reliability was significantly improved.
9.2. Case Study 2: Extending Bearing Life in a Chemical Plant
A chemical plant implemented a comprehensive contamination control program in its steam turbines. This program included advanced sealing solutions, improved filtration, and regular oil analysis. As a result, bearing life was extended by 40%, and maintenance costs were reduced.
9.3. Case Study 3: Improving Turbine Efficiency in a Manufacturing Facility
A manufacturing facility implemented advanced sealing solutions in its steam turbines, reducing steam leakage and improving turbine efficiency. As a result, energy consumption was reduced by 10%, and operating costs were lowered.
These case studies demonstrate the practical benefits of implementing advanced sealing solutions and contamination control strategies in steam turbines.
10. Future Trends in Steam Turbine Technology
Steam turbine technology continues to evolve, with ongoing research and development focused on improving efficiency, reliability, and sustainability.
10.1. Advanced Materials
The development of advanced materials, such as high-strength alloys and ceramic coatings, is enabling the design of more efficient and durable steam turbines. These materials can withstand higher temperatures and pressures, allowing for improved performance and longer service life.
10.2. Digitalization and Monitoring
Digitalization and advanced monitoring technologies are transforming steam turbine maintenance. Real-time monitoring of turbine performance, lubricant condition, and other parameters allows for early detection of potential problems and proactive maintenance, reducing downtime and improving reliability.
10.3. Sustainable Practices
Sustainable practices, such as waste heat recovery and the use of renewable energy sources, are becoming increasingly important in steam turbine technology. These practices help reduce energy consumption, minimize environmental impact, and promote sustainable power generation.
11. Frequently Asked Questions (FAQ) About Steam Turbine Technology
1. What is a steam turbine, and how does it work?
A steam turbine is a mechanical device that converts the thermal energy of steam into mechanical work. High-pressure steam is directed onto turbine blades, causing the rotor to spin and drive a generator or other equipment.
2. What are the key components of a steam turbine?
The key components include nozzles, blades, rotor, casing, bearings, seals, and control system.
3. What are the different types of steam turbines?
Types include impulse turbines, reaction turbines, condensing turbines, non-condensing turbines, and extraction turbines.
4. Why is lubrication important in steam turbines?
Lubrication minimizes friction and wear between moving parts, dissipates heat, and protects against corrosion.
5. What are the common sources of contamination in steam turbines?
Sources include airborne particles, water, process fluids, and wear debris.
6. How can contamination be prevented in steam turbines?
Methods include sealing, filtration, desiccation, and proper maintenance practices.
7. What are bearing protector seals, and why are they important?
Bearing protector seals prevent the ingress of contaminants such as water and dust into the bearing housing, extending bearing life and preventing failures.
8. What is the difference between lip seals and rotating labyrinth seals?
Lip seals are simple and inexpensive but prone to wear. Rotating labyrinth seals offer better protection against contamination and are suitable for high-speed applications.
9. How does lubricant viscosity affect bearing life?
Maintaining the correct viscosity ensures adequate lubrication and prevents wear. A viscosity ratio of less than 1 can reduce bearing life.
10. What are some future trends in steam turbine technology?
Future trends include advanced materials, digitalization and monitoring, and sustainable practices.
12. The Role of CONDUCT.EDU.VN in Understanding Steam Turbine Technology
At CONDUCT.EDU.VN, we understand the challenges you face in finding reliable information about steam turbine technology and best practices. That’s why we’ve compiled a comprehensive resource of articles, guides, and expert advice to help you optimize your steam turbine operations.
Whether you’re an engineer, technician, or manager, our platform provides the knowledge and tools you need to ensure the efficient and reliable performance of your steam turbines. We offer detailed insights into lubrication, sealing solutions, contamination control, and other critical aspects of turbine technology.
Don’t let the complexities of steam turbine technology hold you back. Visit CONDUCT.EDU.VN today to explore our extensive collection of resources and discover how we can help you achieve optimal performance and longevity for your steam turbines.
Contact us:
Address: 100 Ethics Plaza, Guideline City, CA 90210, United States
Whatsapp: +1 (707) 555-1234
Website: conduct.edu.vn
By understanding and implementing the principles and practices outlined in this practical guide, you can significantly improve the reliability, efficiency, and sustainability of your steam turbine operations.